ВЫДЕРЖКА:
Прорыв ТБМ на ГЭС Рёссога 10 декабря 2015 г. первый прорыв ТБМ в Норвегии за более чем 20 лет стал фактом. ТБМ Роббинс доставлен в качестве первой сборки на месте (OFTA) в январе 2013 года и был готов к бурению менее чем через 11 месяцев после
когда был заключен контракт. Во время раскопок ТБМ наткнулся на чрезвычайно твердую породу (более 280 МПа), что представляло серьезную проблему как для ТБМ, так и для резцов. Во время раскопок А. Также в тоннеле была произведена высокоэффективная замена коренных подшипников. Несмотря на то, что проект столкнулись с некоторыми проблемами, производительность ТБМ неуклонно увеличивалась до уровня около 200 м/нед. ближе к концу проекта. После завершения ТБМ прошла обратно через туннель и
разбирается на поверхности.
1. ВВЕДЕНИЕ
Проект гидроэлектростанции Рёссога изначально был построен в 1950-х годах для подачи электроэнергии на железо и алюминиевый завод в близлежащем муниципалитеты. Оригинальная Рёссога ГЭС мощностью 250 МВт. в дополнение к металлургическим работам он предоставил электричество для 19 близлежащих муниципалитетов и сделал
можно электрифицировать железную дорогу Нордландсбанен линия. Завод состоял, среди прочего, из 8-километровый головной тоннель из Норвегии второе по величине озеро, Рёссватнет, по мощности станция рядом с устьем реки Рёссога и на строительство ушло более десяти лет. В начале 2010-х владелец проекта, Statkraft, начата реконструкция электростанции. увеличить мощность до 350 МВт и заменить оригинальные турбины. Это увеличит ежегодный производство силовой установки примерно на 200 ГВтч, в результате чего годовой объем производства составляет 2150 ГВтч. В рамках ремонта также было принято решение отремонтировать головной тоннель с помощью Это также позволяло силовой установке работать на полную мощность. производства при строительстве нового
головной туннель. В качестве примечания отводной туннель был также перемещен выше по реке в увеличить длину очень важных лососевых части реки, что позволяет увеличение выработки электроэнергии с положительным воздействия на окружающую среду. (Статкрафт 2016) Проходческие работы состоят из 7400 м основной головные туннели. Кроме того, было принято решение пробурили подъездной туннель с уклоном 10% и
радиус поворота 500м. Так же и проект включая строительство новой подземной электростанции станции и другие тоннельные работы, связанные с новая электростанция.
Геологический отчет по проекту показал типы пород, которые были благоприятны для механизированных раскопки, в том числе сланцы, слюдяные гнейсы, мрамор, известняк и одна зона, состоящая из граниты (см. рис. 1).
Опыт предыдущих раскопок туннели и наблюдения с поверхности выявленные проблемы с попаданием воды, а также наличие умеренно карстовых элементов. Проект представлен в виде буровзрывных работ проект в мае 2012 года. Подрядчик Leonhard Нильсен ог Сённер (LNS) к тому времени работал с поставщиком ТБМ Robbins, чтобы предложить ТБМ
решение как альтернативный метод строительства. После рассмотрения и согласования тендерных предложений Альтернатива ТБМ признана лучшей экономичный вариант. было несколько важных факторы, лежащие в основе этого решения. Вариант сохранен
несколько километров штольней; они могли уменьшить сечение почти на 40% за счет
увеличение расхода воды в тоннеле ТБМ; и снижается риск повреждения существующих
сооружения, в том числе существующий верхний бьеф туннель, который был в полном объеме, избегая взрывные работы в уязвимых местах. Контракт между Statkraft и LNS были подписаны в ноябре 2012 г. и ознаменовало возвращение ТБМ в Норвегию после
более 20 лет с момента последнего проекта ТБМ.
2. ТБМ ДИЗАЙН
LNS подписала соглашение с Robbins Компания по поставке главной балки 7,23 м ТБМ (МБ-ТБМ) и конвейерная система в Январь 2013 г. У AS LNS не было предыдущих опыт эксплуатации ТБМ Роббинс стремится к обширному обслуживанию и поддержке соглашение на проект.
2.1 Технические характеристики ТБМ
Отремонтированный Robbins MB 236-308 был выбрали для проекта. ТБМ был зарекомендовал себя в холодном климате, предварительно просверлив
более 10 км туннелей для Карахнюкара Гидроэлектростанция в Исландии. ТБМ
явно процветал в холодных условиях, так как установил несколько производственных мировых рекордов, в том числе лучший дневное и недельное производство в своем размерном классе: 115,7 м и 428м соответственно. (Роббинс, 2010 г.) TBM был разработан в соответствии с Robbins HP. принципы с большими резцами, высокой мощностью и
мощная базовая структура. Эти особенности были считается необходимым в отенциально хард-роке Условия выравнивания тоннеля.
2.2 Конструкция скальной крепи и водоотвода
На ТБМ были установлены два перфоратора. Подвижные на 180 градусов кольца для анкерной крепи как можно ближе к переднему щиту, а также одно зондовое сверло на 360-градусном кольце. Кроме того, интегрирована система поддержки крыши McNally
в передний щит для эффективной установки рок поддержка. Основная каменная опора
методика состояла из анкерных болтов и Планки McNally для основной поддержки (см. рис. 2). На мосту был установлен торкрет-робот. появилась возможность нанесения ручного торкретирования в область L1, если требуется более мощная поддержка.
Подготовить ТБМ к обнаружению карстовых условия, Роббинс и норвежская компания
Bever Control разработал специально разработанный Программа измерения во время бурения (MWD) для ТБМ. Это было установлено на Montabert Зондовое сверло HC 110 с питателем, поставляемое Andersen Mekaniske Verksted (AMV). TBM также имел возможность установить дополнительное зондовое сверло при необходимости.
Система измерения во время бурения (MWD) обеспечена электронная визуализация зондового сверла данные в кабине оператора. Данные MWD автоматически анализировались в офис и перевод с TBM производительность в геологической модели, как задано ниже на рисунке 3.
2.3 Конвейерная система
Роббинс также поставил первый непрерывный конвейерная система для использования с ТБМ в Норвегия для проекта. Конвейерная система состоял из туннельного конвейера длиной 7850 м, который также нужно было возить гадость через подъезд туннель и к укладчику. Перспектива запуск конвейера на склоне 1/10 с радиус кривой r=500 является сложной задачей для любого конвейерной системы и может привести к чрезмерному
повреждение ремня. Чтобы избежать этого, Роббинс использовал запатентованный саморегулирующийся натяжной ролик. Кривая натяжной ролик и конвейерная система хорошо зарекомендовали себя на проект и ограничил время простоя конвейера
системы к минимуму, что в значительной степени способствует хорошее производство по проекту.
3 ПЕРВАЯ ДОСТАВКА НА МЕСТЕ
В связи с ограниченными сроками строительства
проекта было решено использовать OFTA (Onsite Первая сборка). ОФТА было разработан компанией The Robbins Company на основе опыт большого количества проектов во всем мире. Вместо традиционного методика отгрузки всех компонентов в один место для полной сборки мастерской, OFTA методология основана на выполнении основных узлов
в мастерской и доставка меньше компоненты непосредственно на объекте для первого полного сборка на месте. Была использована методика в десятках проектов по всему миру и сэкономил значительные временные и трудовые затраты. Для ТБМ Rossaga сборочный узел был собраны в Италии и отправлены на место. Первый крупный
части прибыли на место 30 августа 2013 года. Хорошая команда, состоящая из специалистов Robbins и Сотрудники LNS произвели эффективную сборку, несмотря
проблемы с погодой и снегом во время сборки (см. рис. 4 и 5). ТБМ и
резервные порталы собраны и готовы к бурению к середине декабря 2013 г.
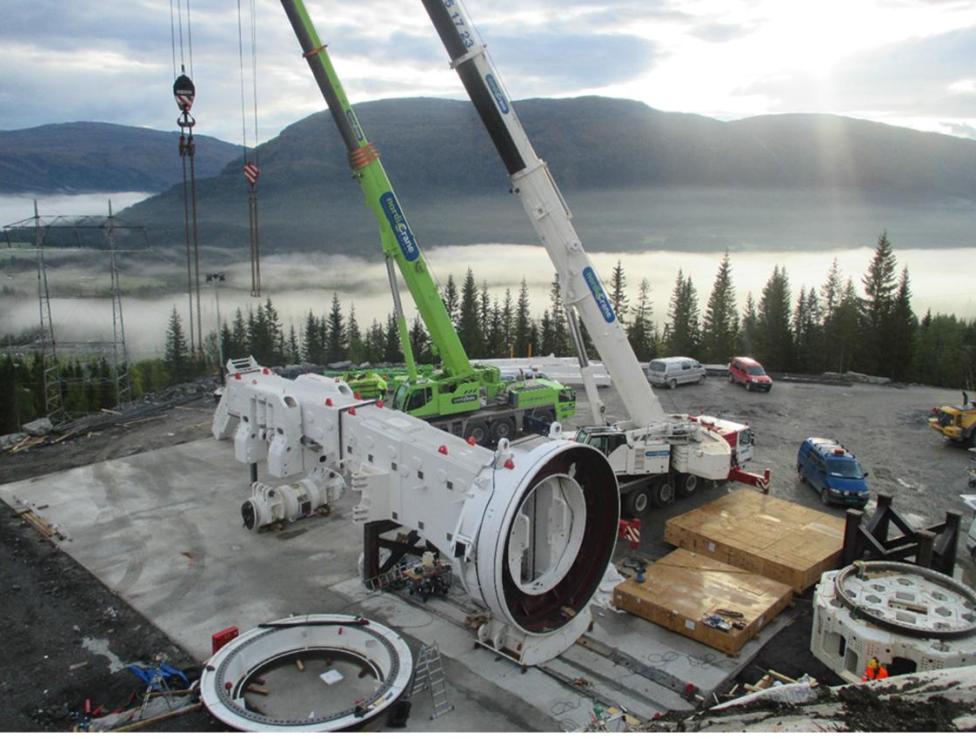
Рисунок 4. Сборка OFTA в Россоге (Gibson 2013)
ТБМ Rossaga был заказан в конце января. 2013 год и машина была в принципе готова к
скважина на участке в декабре 2013 г. Фактически машина была готова к растачиванию менее чем за 11 месяцев после подписания контракта.
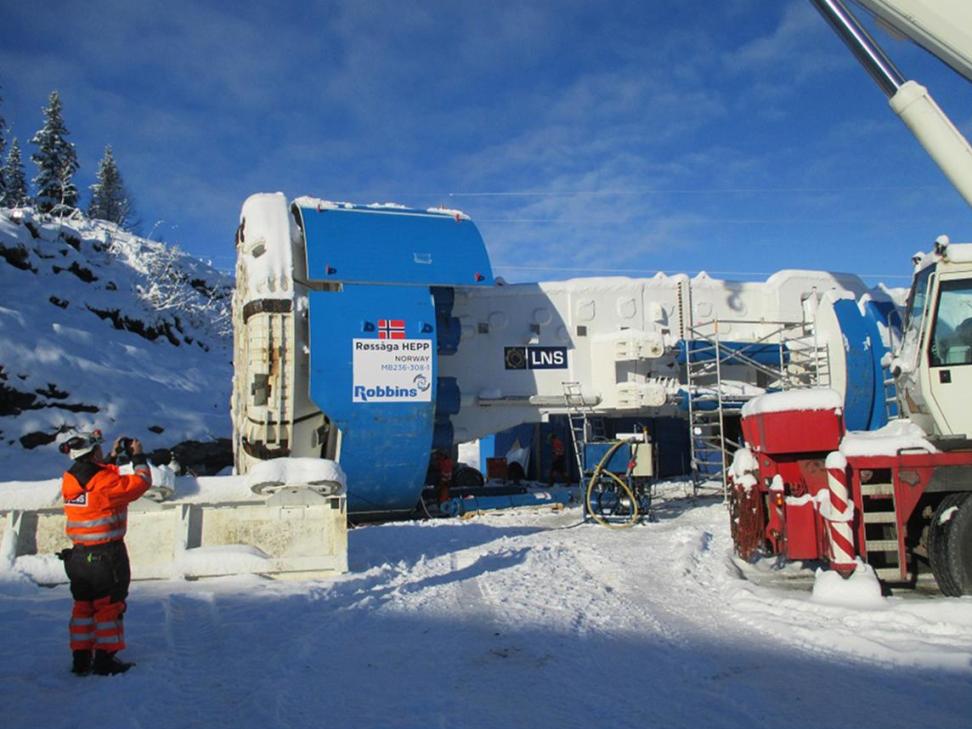
Рисунок 5. Собранная ТБМ на снегу (Solhaug 2013) |
4 РЕЗУЛЬТАТЫ ПРОЕКТА
4.1 Производство
Первоначальный план проекта состоял в том, чтобы собрать ТБМ на поверхности и спуститесь на стартерная камера на гл.450. После первоначального Учитывая это, было принято решение о бурении 450 м. длинный подъездной туннель с поверхности.
сочетание неожиданного хард-рока, кривизны, обучение персонала, корректировка
ТБМ и конвейерно-строительные работы (монтаж конвейерной кассеты и выемки 300м
тоннель D&B от тоннеля TBM), вызвал производство будет медленным. Более стабильную работу делал не произойдет, пока машина не окажется в начале головной туннель.
После первоначального запуска производство стабилизировалось в очень твердая порода с несколькими месяцами снижения производство из-за непредвиденных инцидентов (см.
Рисунок 6). Среди них поврежденный захват колодка и ремонт в декабре 2014, коренной подшипник замена в марте/апреле 2015 г. и тяжелые притока воды в ноябре 2015 г. Все эти три События будут описаны далее в статье. Также стоит отметить, что июль, декабрь
и март/апрель имеют меньше часов работы из-за норвежских праздников. После первоначальной очень твердой породы проходимость улучшилось в октябре 2014 года, и это, вместе с более квалифицированный экипаж, способствовал более эффективному
операция. По истечении этого срока производство стабилизирован на высоте 500 м и выше в производстве месяцев, с месячными максимумами выше 800м. Стоит отметить, что высокая производительность стало возможным благодаря квалифицированным рабочим и хорошему сотрудничество между Роббинс и LNS персонал на месте. Эффективность очевидна проиллюстрировано впечатляющими ежедневными и еженедельными производственные рекорды, 52 м и 250 м соответственно, в очень твердом и сложном скальном массиве.
4.2 Чрезвычайно хард-рок
Сразу после того, как ТБМ начал скучать, чрезвычайно твердая порода со средней прочностью породы свыше 200 МПа и некоторые зоны с повышенной прочностью
встречались более 280 МПа (см. рис. 7). Кроме того, скала была массивной с очень
ограниченная трещиноватость, с классами гидроразрыва NTNU ниже St. I- и высокоабразивные с Cutter Life Значения индекса (CLI) в диапазоне от 4,5 до 11 и
в среднем чуть выше CLI=5.
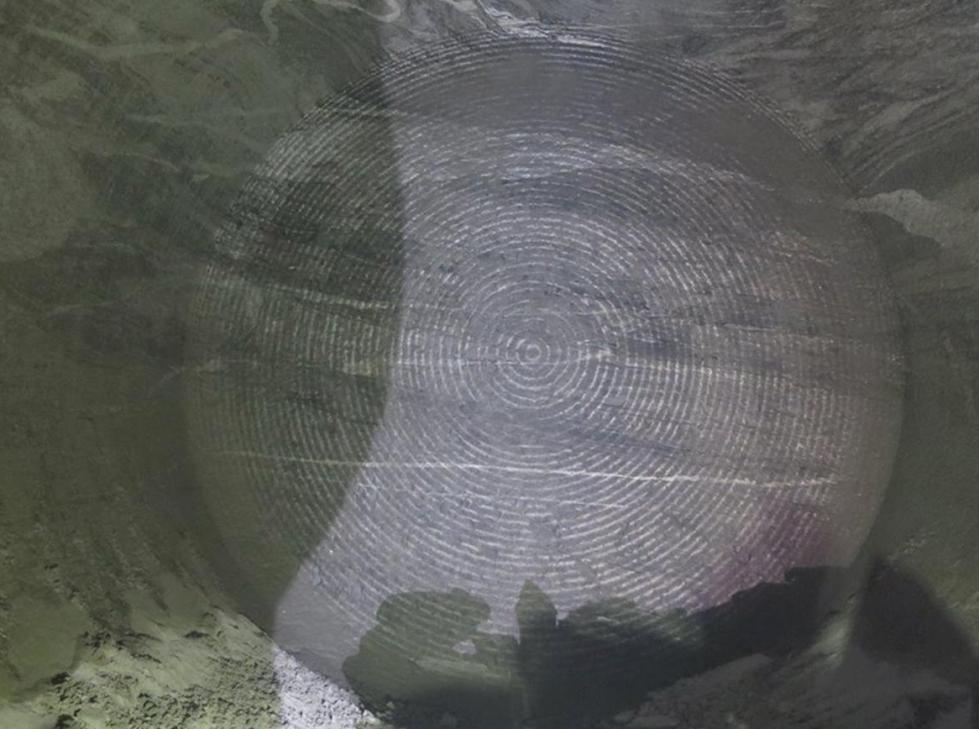
Рисунок 7. Чрезвычайно массивная и нетрещиноватая режущая поверхность (Андерсон)
Сочетание кривизны, наклона и экстремальные свойства горных пород означали некоторые из самые сложные условия бурения для любой ТБМ и поставил бы любой ТБМ и любой резец на окончательный тест. Экстремальные условия привели к снижению
срок службы фрезы (примерно 100-150 м3/резак), что снова сказалось на производстве
проект. Чтобы исправить ситуацию, Роббинс отдел резки принял участие и сделал подробный анализ геологии, производительности машин, износ резца и механизмы поломки резца. Основанный на по результатам анализа резака отдел работал вместе со стальным поставщика и цеха термообработки для оптимизации свойства режущего кольца в зависимости от встречающейся геологии.
Огромный опыт компании Robbins и лет экспериментов со стальными сплавами и
обработках, разрешили отделу резки делать квалифицированные соображения и разработка некоторых различные режущие кольца со свойствами, которые могут
увеличить срок службы фрезы. После первоначальных испытаний с несколько различных материалов/термических обработок, которые выступили хорошо, одна из версий, XHD4,
выделился и показал очень многообещающее сокращение разрушительного износа колец. XHD4 фрезы используют те же сплавы, что и мир знаменитые кольца Robbins HD, однако есть изменения в процессе термообработки, которые улучшает свойства кольца в чрезвычайно хард-рок, как на Rossaga. Усовершенствование режущих колец XHD4
трудно оценить проект из-за постепенное внедрение новых фрез и изменения в геологии, но вполне вероятно, что производительность на очень сложных участках улучшить не менее чем на 25%. Преимущества XHD4 также, вероятно, объясняет превосходство
срок службы резака до конца проекта, а также в относительно мягкий грунт.
Геология всего проекта была обычно массивные, очень твердые и абразивные для
большую часть туннеля. На основе испытаний горных пород и выполнено картографирование первых 5200 м туннеля NTNU было замечено, что 80% туннеля
имели значения CLI ниже CLI=10 и более 30% имели значения CLI ниже CLI=6. Для справки
это типичные значения, которые вы видите в очень жестких типы горных пород, такие как невыветренные граниты или кварцит. В дополнение к испытанию горных пород, NTNU
выполнено геологическое картирование проекта. В частности, первые 5200 м показывают очень последовательный диапазон трещиноватости от KS=0,43 до KS = 0,59 (Масиас, 2014 г.), что соответствует среднее расстояние между разрывами более чем 100см. Первые 2 км скала была постоянно около 200 МПа и выше, в то время как между 2км -5км скала была между 100- 200 МПа, на некоторых участках выше 200 МПа. Остальная часть туннеля была проверена на прочность. около 100 МПа и выше.
На основании испытаний горных пород и геологических сопоставление NTNU-модели оценило сеть скорость проходки по проекту 1,37 м/ч и срок службы фрез всего 88 м3/c на первых 5200 м проекта (Бруланд, 2015). Это иллюстрирует в определенной степени чрезвычайно сложный характер встреченного массива горных пород. Для того же
длина туннеля фактическая чистая скорость проходки составляла 2,12 м3/ч, ресурс резца 284 м3/с. При включении последних 2 км туннеля чистая скорость проходки увеличивается до 2,22 м/ч и ресурс фрезы до 306 м3/c. Большие отклонения расчетной и фактической производительность, вероятно, будет объяснена тестом образцы не являются полностью репрезентативными встречающаяся геология и что NTNU
модель может недооценивать производительность современные ТБМ для твердых пород. Однако, очевидно что ТПМ и резцы выполнили чрезвычайно хорошо в геологии встречается.
4.3 Замена коренных подшипников
Вечером 14 февраля 2015 г. экипажи выявлено загрязнение в коренном подшипнике
полость, которая могла указывать на коренной подшипник наносить ущерб. ТБМ был немедленно остановлен на дальнейший анализ, включая зондовую камеру инспекции. Проверки не дали окончательных результатов ответы и владелец, подрядчик и
производителю необходимо рассмотреть возможность выполнения эффективная замена коренных подшипников или продолжение ствол с риском дальнейшего повреждения ТБМ и, возможно, полный отказ подшипника. После тщательных размышлений было принято решение поменять коренной подшипник. Решение было поддерживается вероятностью эффективного замена, в связи с тем, что был Возможна замена основного подшипника. LNS является опытный подрядчик D&B с оборудованием и персонал, доступный на объекте, и Роббинс имел имеется опытная команда выездного обслуживания, которая снизит риск любых задержек в работе. Решение было принято в четверг на той неделе и подготовка к отправке замены вынос на площадку и начаты взрывные работы в нише немедленно. Подробный и агрессивный план произведена замена: Планировалось завершить замену в течение шести недель и быть скучно к концу марта, перед Пасхой каникулы. Процедура замены коренного подшипника для ТБМ с главной балкой в ??туннеле выглядит следующим образом:
1) Взорвать нишу длиной 25 м и высотой 3,5 м.
в венец позади ТБМ и установить подъемный
оборудование.
2) Открутите текущую режущую головку и прикрутите его к стене туннеля.
3) Ввести новый основной подшипник и повесить в нишу.
4) Прогулка по ТБМ обратно в нишу.
5) Замените коренной подшипник и повесить старый коренной подшипник в нишу.
6) Прогулка TBM до забоя туннеля и болт на ножевой головке Фигура
7) Снимите все основные компоненты подшипника и повторно подключить ТБМ.
8) Готов к бурению.
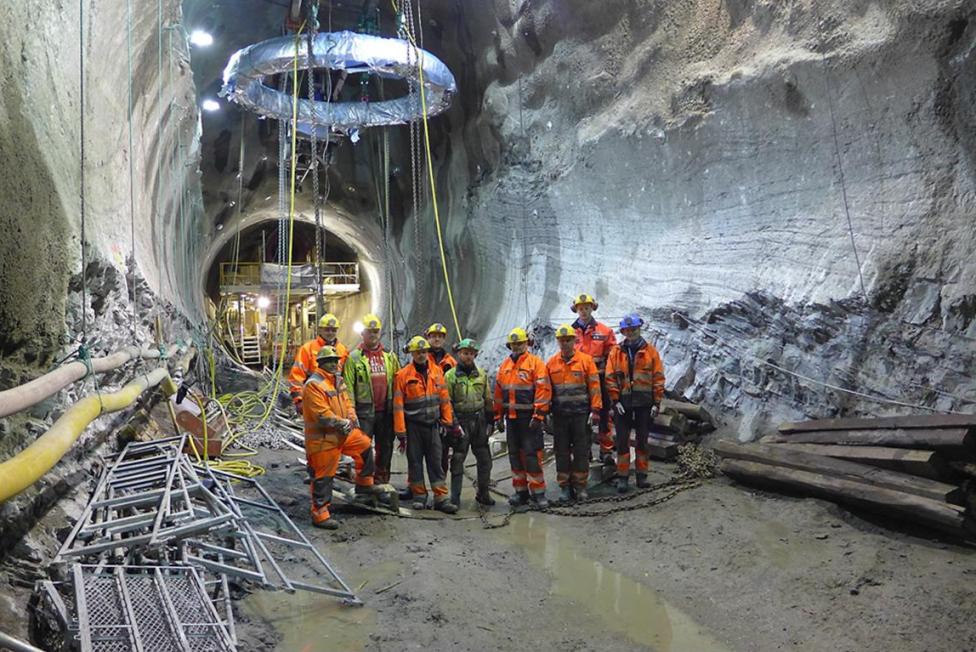
Коренной подшипник перевозился на грузовике из Германии и уже был готов на месте на
2 марта, менее чем через две недели после принято решение о замене коренного подшипника.
Это было за два дня до окончательного оформления ниши. и установленное грузоподъемное оборудование (см. рис. 8).Благодаря тесному сотрудничеству между
опытные туннелисты LNS и опытный Роббинс Персонал полевой службы при участии старшего Персонал Statkraft, коренной подшипник был заменены, и машина начала скучно на 30 марта, менее чем через шесть недель после принятия решения на замену был взят коренной подшипник. К знаний авторов, это один из самых быстрых замены коренных подшипников, когда-либо выполненные на ТБМ этого размера. |