Технологии усовершенствования шарошек
для микротоннелирования
|
АБСТРАКТНЫЕ
Для ТБМ в твердых породах два наиболее важных параметра, которые следует учитывать, — это производительность резца и скорость проходки. Эти два фактора сильно зависят друг от друга, поскольку резцы обычно являются критическими компонентами, которые ограничивают тягу машины — критическая переменная, определяющая чистую скорость проходки. В таких условиях оптимальная производительность резцов чрезвычайно важна не только для оптимизации эффективной скорости проходки, но и для минимизации времени, необходимого для смены резцов, и увеличения времени, доступного для бурения. За последние пять лет в разработку фрез были вложены огромные средства, чтобы сделать фрезы способными выдерживать даже самые сложные условия. В этом документе будут представлены раз
работки и проблемы, которые привели к развитию технологий резки за последние годы, а также результаты этих разработок в последних проектах.
Экстремальные условия для фрез могут привести к плохой скорости подачи, катастрофическому отказу дисковой фрезы или неприемлемому сроку службы дисковой фрезы. Сюда относятся не только условия в твердых породах, но и условия в скалах и смешанном грунте под уровнем грунтовых вод. Дисковые резаки — это зрелая технология, и возможности ее усовершенствования ограничены; любые реализованные улучшения, вероятно, будут дополнительными для прогресса и стоимости любого проекта в экстремальных условиях.
Чрезвычайно твердая порода считалась ограничивающим фактором для выемки твердых пород с тех пор, как в 1952 году была использована первая успешная ТБМ для твердых пород. Проблемы, связанные с постепенно твердеющей породой, и соответствующая потребность в большем усилии для создания пропила послужили толчком к развитию. от фрез к дисковым фрезам, а затем к фрезам постепенно большего размера. Это постоянное увеличение размера в конечном итоге привело к внедрению 19-дюймовых резцов на гидропроекте Свартисен в 1988 году для бурения чрезвычайно твердых норвежских пород. Это введение 19-дюймовых фрез означало, что несущая способность преодолела предел качества стали. Сегодня 20-дюймовые дисковые фрезы являются отраслевым стандартом для твердых пород. Как показывают события, описанные выше, проблемы и опыт, возникающие на участках, исторически способствовали развитию фрез. Тем не менее, за последние пять лет в рамках нескольких параллельных исследований проводились исследования и разработка более совершенного режущего инструмента. Эти проекты включали обширную исследовательскую программу с Университетом Тронхейма, Норвегия (NTNU) и систематическое сотрудничество с долгосрочными поставщиками для оптимизации и разработки существующих сплавов и металлургических процессов, используемых в кольцевой стали.
Твердая порода под давлением воды является еще одной областью развития: в Нью-Йорке, США, в Делавэрском ремонте акведука, ТБМ с одним экраном будет бурить скалу при давлении воды до 20 бар. Дисковые фрезы диаметром 19 дюймов будут использовать компенсацию давления, которая была протестирована до 34 бар для земляных работ под высоким давлением. В документе также будут представлены как результаты лабораторных испытаний, так и первые результаты проекта.
1. ВВЕДЕНИЕ
1.1.История
С тех пор, как в 1952 году в рамках проекта строительства плотины Оахе в Южной Дакоте, США, была запущена первая действующая ТБМ, режущие инструменты были операционным ограничением для работы ТБМ. Производительность ТБМ была улучшена с изобретением вращающегося дискового резца в канализационном туннеле реки Хамбер в Канаде в 1956 году, но режущие инструменты до сих пор являются ограничивающим фактором для работы ТБМ в очень твердых породах.
В начале 1980-х были представлены дисковые фрезы диаметром 14 и 15,5 дюймов. 15,5-дюймовый резак был усовершенствованием по сравнению с 14-дюймовым за счет большего набора подшипников и соответствующего увеличения осевого усилия. Вскоре после этого 15,5-дюймовая фреза была увеличена до 17 дюймов за счет установки диска большего диаметра на тот же комплект подшипников. Хотя сила тяги фрезы не изменилась, предполагалось, что 17-дюймовый диск с увеличенным жертвенным материалом увеличит среднее время между заменами фрезы. Это подтвердилось, и 17-дюймовая фреза стала стандартом де-факто даже после того, как в конце 1980-х годов для гидроэлектростанции Свартисен в Норвегии была разработана 19-дюймовая фреза.
TBM, используемые в Svartisen, были первыми TBM с «высокой производительностью» (HP). Эти ТБМ HP были разработаны с увеличенной тягой и мощностью режущей головки по сравнению с более ранними машинами. В то время как 19-дюймовая фреза отличалась повышенной силой тяги, материал диска, исторически использовавшаяся хромированная/молибденовая/никелевая сталь, не соответствовал этой задаче. Только с появлением инструментальной стали, а затем модифицированной инструментальной стали, можно было использовать преимущества увеличенной тяговой способности. Тем не менее, в чрезвычайно твердых породах сталь резцов по-прежнему является ограничивающим фактором в работе, поэтому это по-прежнему находится в центре внимания для улучшения свойств стали режущих колец.
В последующие годы 20-дюймовые дисковые фрезы стали самыми современными в условиях очень твердых пород.
1.2.Теоретическая основа
Опыт, который Роббинс получил на месте, показывает, что использование больших резцов с высокими нагрузками в условиях очень твердых пород дает очевидные преимущества. Использование более крупных резцов дает два явных преимущества: более высокое осевое усилие и более длительный срок службы.
Более высокая мощность тяги позволяет эффективно бурить более твердые породы. Чтобы эффективно резать горную породу, осевое усилие, прикладываемое к отдельному резцу, должно преодолевать сопротивление проникновению горной породы и инициировать образование стружки. Как только критическое давление достигнуто, проникновение быстро увеличивается при относительно небольшом увеличении нагрузки на резец. Критическое давление увеличивается с увеличением прочности породы, и именно по этой причине были разработаны более крупные резцы для бурения более твердых пород. Этот принцип проиллюстрирован на рисунке 1.
Более длительный срок службы является результатом увеличения объема расходуемого материала в дисковом кольце большего диаметра. Переход с 19 дюймов на 20 дюймов на том же сердечнике подшипника основан на том же принципе, что и усовершенствование 15,5-дюймовой фрезы путем установки 17-дюймового диска большего диаметра еще в 1980-х годах. Относительные объемы износа 17-, 19- и 20-дюймовых дисков сравниваются на рисунках 2
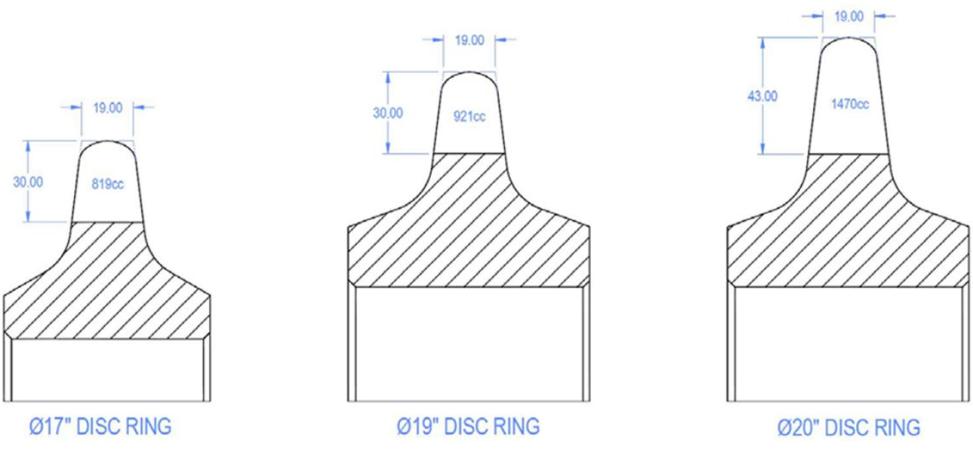
Рис. 2. Сечение режущих колец и расчет объема износа.
Поперечные сечения 17-дюймового и 19-дюймового фрез практически идентичны, если рассматривать только расходуемую часть или «лезвие» диска. На рис. 2 предполагается износ 30 мм для размеров 17 и 19 дюймов, и даны относительные объемы износа. У 19-дюймового диска объем износа на 12% больше, чем у 17-дюймового диска. Однако 20-дюймовый диск имеет значительно больший объем износа (60%) по сравнению с 19-дюймовым кольцом. Наконечник 20-дюймового диска был расширен на 13 мм по радиусу по сравнению с 19-дюймовым диском, в то время как остальная часть профиля диска осталась неизменной.
Тот же принцип удлиненных дисков наконечника может быть применен к 17-дюймовому резцу, и, когда позволяет геология, многие операторы ТБМ выбирают 18-дюймовый диск или даже 19-дюймовый диск, установленный на 17-дюймовом несущем сердечнике, чтобы преимущество добавленного жертвенного материала. Это может быть эффективным решением при проходке забойных тоннелей под давлением, позволяющим увеличить время между работами с режущей головкой.
Другим важным аспектом фрез является ширина кончика фрез. Более узкая ширина режущей кромки увеличит давление под резцом и сделает дробление породы более эффективным. Однако меньшая ширина наконечника также снижает объем износа дискового кольца и увеличивает нагрузку на режущие кольца. В очень твердых горных породах, когда резцы работают на пределе своих возможностей, обычно наблюдается некоторый разрушительный износ, такой как грибовидное образование и выкрашивание по краям режущего кольца. Это не является серьезной проблемой до тех пор, пока разрушающий износ не станет доминирующим механизмом износа резцов и/или износ резцов не достигнет вредного уровня. Исторически сложилось так, что лучшим компромиссом между желанием иметь меньшую ширину наконечника и приложенным давлением под фрезой были кольца с шириной наконечника ? дюйма (19 мм). Этот компромисс зависит от сочетания абразивных свойств стали и ее способности выдерживать высокие нагрузки или удары. Среди производителей резцов общепринятой практикой является либо увеличение ширины вершины, либо увеличение боковых углов режущего кольца для увеличения контакта с горной породой и снижения напряжений в режущих кольцах за счет увеличения материала, который может изнашиваться. Это, в дополнение к абразивным свойствам стали режущего кольца, делает очевидным, что дальнейшая разработка материала стали кольца важна для повышения производительности в условиях очень твердых пород.
2. МЕТАЛЛУРГИЯ И ФОРМА КОЛЬЦА ДЛЯ ЧРЕЗВЫЧАЙНО ТВЕРДЫХ И АБРАЗИВНЫХ ПОРОД
2.1.Металлургия
Большинство производителей дисковых колец производят кольца из одной из высоколегированных сталей, известных под общим названием «инструментальные стали», и эти стали могут быть либо стандартными, либо модифицированными. В дополнение к указанию химического состава стали микрочистота также должна контролироваться спецификацией метода производства. Обычная производственная последовательность включает плавку, литье, прокатку, ковку, черновую обработку, термообработку и окончательную обработку.
После того, как стальной расплав был отлит и затвердел в слитки, он перемещается в прокатный стан, где повторно нагревается и прокатывается в гораздо более длинный прямоугольный или круглый стержень со значительно уменьшенным поперечным сечением. Высоколегированные стали склонны к ликвации сплава в отлитом слитке, и механическая прокатка и уменьшение площади служат для смягчения такой ликвации.
Длинные стержни нарезаются по длине, а затем выковываются в кольца. Критическое значение в процессе ковки имеет падение температуры стали. Процесс ковки должен быть завершен достаточно быстро, чтобы получить желаемую форму при сохранении температуры детали в пределах оптимального диапазона ковки. Внутренние дефекты в кольце возникнут, если температура упадет ниже оптимальной. Роббинс предпочитает автоматизированный метод штамповки в закрытых штампах, хотя в прошлом мы успешно использовали прокатные поковки. Автоматизация, по-видимому, является ключом к стабильному качеству при любом методе ковки.
Механическая обработка и термообработка являются последними этапами. Состав стали и процессы ковки, конечно, важны, но наиболее важным процессом является термическая обработка стали. Термическая обработка изменяет кристаллическую структуру стали и при этом увеличивает твердость и прочность (положительный результат), но в то же время увеличивает хрупкость (отрицательный результат). У хрупкой стали резко снижается вязкость разрушения. Следовательно, очень твердая сталь может выжить в более мягких геологических формациях, но катастрофически потерпеть неудачу в более сложной геологии. Сбалансированная твердость и вязкость разрушения могут быть достигнуты как за счет выбора сплава, так и за счет процессов термообработки.
Компания Robbins недавно усовершенствовала процесс термообработки наших стандартных дисковых колец из инструментальной стали HD, чтобы создать дисковые кольца XHD. Усовершенствования добавляют минимальную стоимость, и результатом является повышенная твердость и повышенная прочность, но без обычно связанного с этим снижения вязкости разрушения.
Диски XHD стандартного поперечного сечения прошли успешные испытания на ТБМ открытого типа, работающих на проекте Rossaga в Норвегии и проекте Yin Han Ji Wei в Китае. Геология обоих проектов состояла из гранитной породы с прочностью от 138 МПа до 300 МПа и содержанием кварца от 43% до 92%.
Предварительные результаты, представленные подрядчиками, показывают, что диски XHD демонстрируют увеличение срока службы резцов более чем на 20% по сравнению со стандартными дисками HD в геологии 200 МПа, где проводились испытания.
2.2. Форма диска
Роббинс изучил среднюю степень износа дисковых фрез и влияние износа на скорость бурения. Мгновенное проникновение примерно пропорционально ширине кончика фрезы. Новые стандартные диски имеют ширину на кончике 19 мм.
Однако, когда они полностью изношены, их ширина на кончике составляет примерно 30 мм при данном угле наклона боковой поверхности. Это происходит из-за бокового угла лопастной части диска. Боковые стороны лопастной части диска не параллельны, а образуют небольшой клин. Этот угол клина может отличаться в зависимости от поставщика фрезы. Анализ износа каждого диска при каждой проверке в 2016 году на ТБМ с главной балкой на проекте Yin Han Ji Wei в Китае показывает, что средний износ составляет примерно 19 мм. (Рисунок 3). Это соответствует средней теоретической ширине наконечника 24 мм (рис. 4).
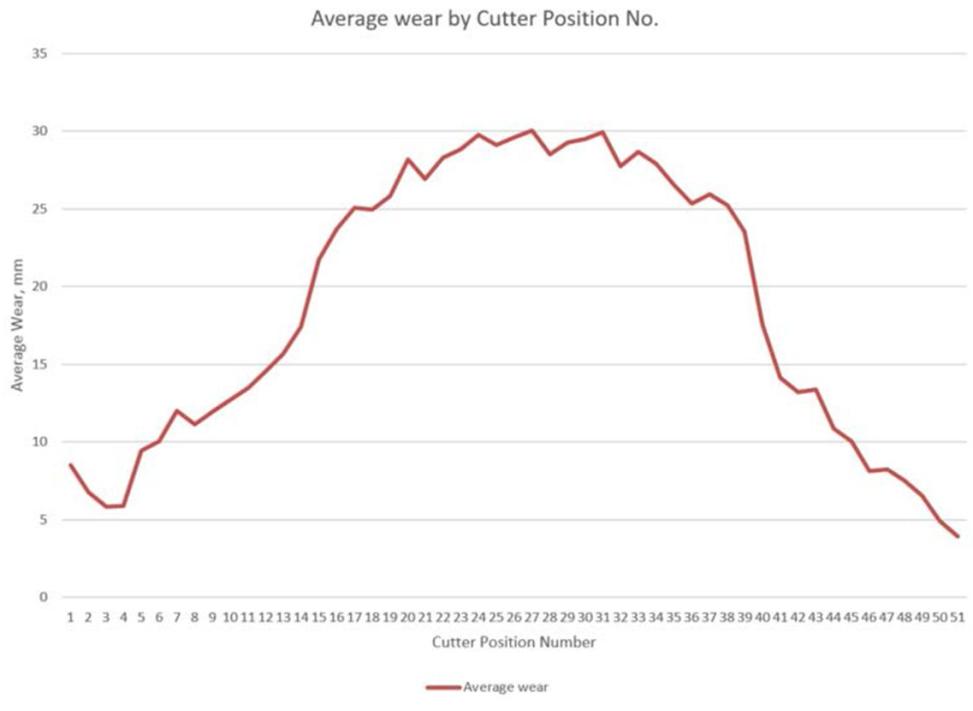
Рис. 3. Средний износ позиций на режущей головке в Yin Han Ji Wei |
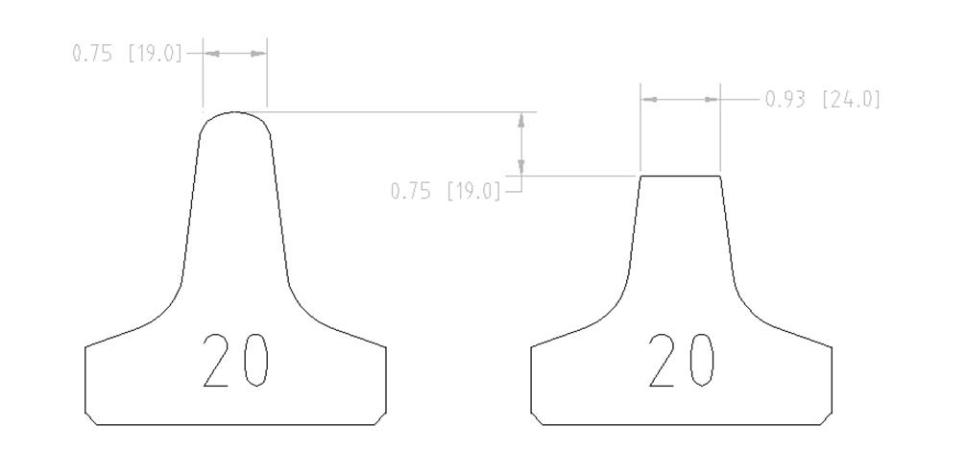
Рис. 4 Иллюстрация наконечника с различными значениями износа
Средняя ширина наконечника важна, поскольку скорость продвижения ТБМ будет уменьшаться по мере увеличения ширины наконечника диска. Например, в гранитной породе 190 МПа:
- Теоретическая скорость продвижения с новыми дисками шириной 19 мм составит 1,36 м/час в массивной несвязанной породе.
- В той же породе, когда ширина наконечника увеличивается из-за износа до 24 мм, теоретическая скорость продвижения снижается до 1,06 м/час.
Это представляет собой значительное снижение производительности ТБМ.
2.3.Улучшенная металлургия и форма
Одним из проверенных решений для увеличения средней скорости проходки является использование дисков с более узкой шириной наконечника. Альтернативным методом может быть уменьшение угла наклона лезвия диска таким образом, чтобы оно расширялось медленнее по мере износа, эффективно оставаясь «острым» дольше. Риск использования диска с уменьшенным углом наклона заключается в том, что механическое напряжение внутри диска будет увеличиваться, что может привести к при объемном гидроразрыве, когда резцы подвергаются ударным нагрузкам. Ясно, что для снижения риска было бы полезно использовать сталь с повышенной прочностью (твердостью) и повышенной вязкостью разрушения.
2.4.Опыт с места: проект Rossaga: тестирование колец XHD
Туннельная часть ТПМ на ГЭС Рёссога в Норвегии состояла из 7400-метровых подводящих туннелей. Кроме того, было принято решение о бурении подъездного туннеля с уклоном 10 % и радиусом кривизны 500 м. Кроме того, проект включал строительство новой подземной электростанции и другие работы по прокладке туннелей, связанные с новой электростанцией. Туннель был прорыт 7,23-метровой MB-TBM, оснащенной 49 19-дюймовыми фрезами.
Сразу после начала бурения ТПМ были обнаружены чрезвычайно твердые породы со средней прочностью выше 200 МПа и отдельные зоны с прочностью выше 280 МПа (см. рис. 5). Кроме того, порода была массивной с очень ограниченной трещиноватостью, с классами трещиноватости по NTNU ниже St. I- и высокоабразивной со значениями индекса стойкости резца (CLI) в диапазоне 4,5-11 и в среднем чуть выше CLI=5.
Экстремальные свойства горных пород и геометрия начальных работ означали одни из самых сложных условий бурения для любой ТБМ и подвергли бы любую ТБМ и резец суровому испытанию. Экстремальные условия вызвали низкий ресурс резцов (примерно 100-150 м3/резец), что снова сказалось на реализации проекта. Чтобы исправить ситуацию, вмешался отдел резцов Robbins, который провел подробный анализ геологии, производительности машин, механизмов износа и отказов резцов. Основываясь на результатах анализа, отдел резки работал вместе с поставщиком стали и цехом термообработки, чтобы оптимизировать свойства режущего кольца в соответствии с геологическими условиями. Опыт компании Robbins и годы экспериментов со стальными сплавами и термической обработкой позволили отделу резцов провести квалифицированное рассмотрение и разработать несколько различных режущих колец со свойствами, которые могут увеличить срок службы резца. После первоначальных испытаний с несколькими различными материалами/термической обработкой, которые показали хорошие результаты, одна из версий, XHD, выделилась и показала многообещающее снижение разрушающего износа колец. В резцах XHD используются те же сплавы, что и в кольцах Robbins HD, однако в процесс термообработки внесены изменения, которые улучшают свойства кольца в чрезвычайно твердых породах, как видно на Rossaga.
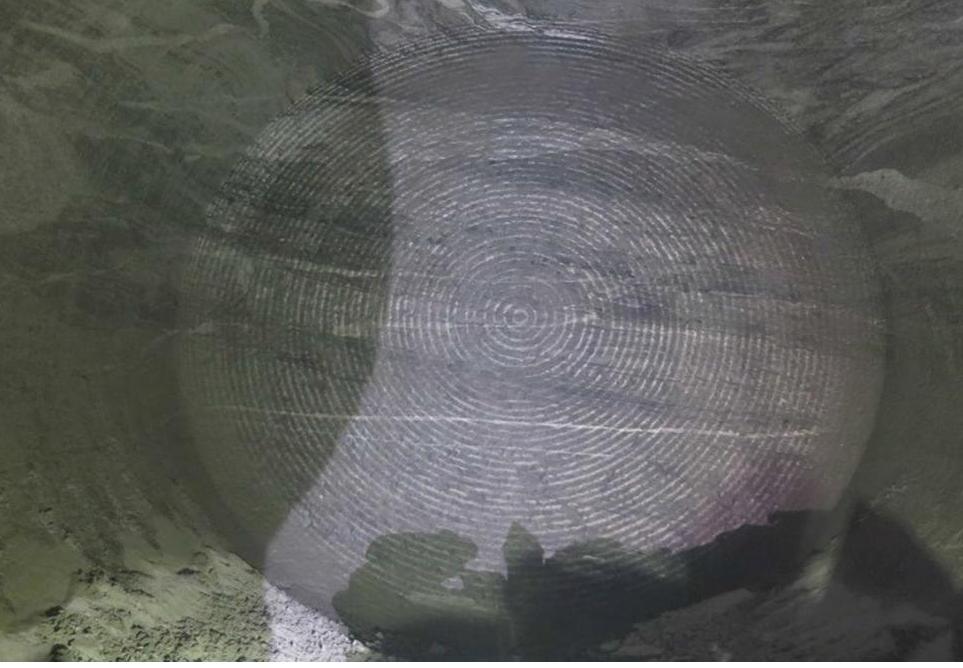
Рисунок 5. Чрезвычайно массивная и нетрещиноватая режущая поверхность.
Улучшение режущих колец XHD трудно поддается количественной оценке в связи с постепенным внедрением новых резцов и изменениями в геологии, но представляется вероятным, что производительность в очень твердых секциях была улучшена как минимум на 25%. Преимущества XHD также, вероятно, объясняют более длительный срок службы фрезы на оставшейся части проекта, даже на относительно более мягком грунте.
Основываясь на испытании горных пород и геологическом картировании, модель NTNU оценила чистую скорость проходки по проекту в 1,37 м/ч и срок службы резца всего 88 м3/с на первых 5200 м проекта). Это в определенной степени иллюстрирует чрезвычайно сложный характер встречающегося массива горных пород. При той же длине туннеля фактическая чистая скорость проходки составила 2,12 м/ч, а срок службы резца – 284 м3/с. При включении последних 2 км туннеля чистая скорость проходки увеличивается до 2,22 м/ч, а ресурс резца до 306 м3/с.
Большие отклонения в расчетных и фактических характеристиках, вероятно, объясняются тем, что тестовые образцы не полностью репрезентативны для обнаруженной геологии, и тем, что модель NTNU может недооценивать характеристики современных ТБМ для твердых пород. Однако очевидно, что ТБМ и резцы показали себя лучше, чем ожидалось, в встреченной геологии.
Также были проведены испытания режущих колец XHD на проекте Yin Han Ji Wei в Китае, который работает в гранитной породе с давлением около 200 МПа. Результаты по состоянию на конец 2017 г. указывают на увеличение срока службы резцов на 23 % по сравнению с кольцом Robbins HD при сопоставимых геологических условиях и эксплуатации машины. Поскольку диски XHD стандартной формы, протестированные в Yin Han Ji Wei, работали значительно лучше, чем отраслевой стандарт, следующим шагом будет производство и тестирование дисков XHD с уменьшенным углом наклона по бокам. Цель двоякая: увеличить скорость проходки за счет уменьшения средней ширины наконечника режущей головки и увеличить срок службы дискового кольца за счет улучшенной металлургии. Первоначальные результаты полевых испытаний очень многообещающие, но окончательные результаты еще не получены.
3. РАБОТА ПОД ВЫСОКИМ ДАВЛЕНИЕМ
Еще одним очень сложным условием, которое стало более распространенным в последние несколько лет, является работа фрезы при высоких давлениях. Одним из примеров этого является ТБМ с одинарным экраном диаметром 6,5 м, оснащенная 19-дюймовыми дисковыми резцами с компенсацией давления для проекта ремонта акведука в Делавэре в США. Для этого проекта требуются резаки, способные выдерживать давление 20 бар.
Роббинс разработал и запатентовал систему компенсации давления для фрез, которая отличается от предыдущих конструкций. В конструкции используется фиксатор с компенсацией давления для работы резцов при повышенных давлениях. Четырнадцать поршней расположены в части держателя уплотнения фрезы, в то время как обычным методом является добавление одного или двух поршней на вал фрезы. Поршни видны на рис. 6 в виде круглой формы снаружи вала, к которому подсоединяется шланг для заливки масла. Поршни, расположенные в держателе, оказались более устойчивыми к засорению, особенно при проходке туннелей в мягком грунте, чем поршни, расположенные внутри вала фрезы. Теоретически резак выдержит любое мыслимое давление, но поскольку мы не использовали этот резак при давлении выше 5 бар, резак был испытан при давлении до 36 бар в наполненном водой испытательном сосуде высокого давления. Были проведены статическое испытание и испытание на вращение под давлением.
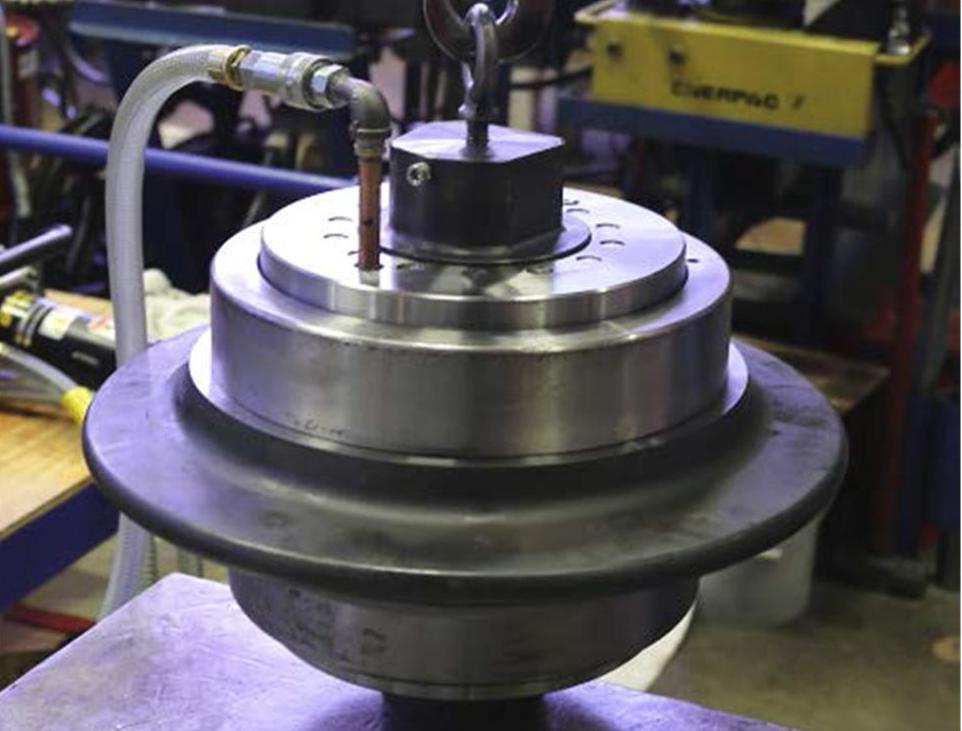
Рисунок 6. Дисковая фреза с компенсацией давления.
3.1.Статическое испытание под давлением
Внешнее давление на резак постепенно повышали до 5,0 бар в течение первой минуты, а затем давление повышали со скоростью 2,0 бар/мин. В конечном итоге давление было поднято до 36 бар, что является максимальной производительностью гидростатического насоса. На рис. 7 представлена зависимость давления внутри и снаружи резца за время испытаний. Внутреннее давление резца было увеличено до уровня, почти равного внешнему давлению в сосуде. Разница оказалась в пределах 0,15 бар.
3.2. Испытание на вращение под давлением
Резак вращали, и скорость постепенно повышалась до максимально возможной скорости двигателя. Фреза достигла 110 об/мин (рассчитано по частотно-регулируемому приводу и зафиксировано с помощью бесконтактного тахометра). Параметры частотно-регулируемого привода записывались при каждом увеличении скорости. На максимальной скорости давление в сосуде увеличивалось с нуля до 5,0 бар за одну минуту и ??регистрировались параметры ЧРП. После этого давление повышали со скоростью 2,0 бар/мин до 20 бар. Вращение фрезы продолжали со скоростью 110 об/мин, а внешнее давление поддерживали на уровне 20 бар в течение 60 минут. В течение этого периода параметры ЧРП и показания давления наблюдались непрерывно и записывались каждые 5 минут. После 60 минут работы давление снова повышали со скоростью 2,0 бар/мин. Давление постепенно повышали, пока оно не достигло максимальной производительности насоса 36 бар.
Результаты показали, что при максимальной скорости фрезы 110 об/мин работа фрезы не влияла, а крутящий момент фрезы не менялся, даже несмотря на то, что давление достигло максимальной производительности насоса 36 бар. Механизм компенсации давления резца уравновешивал внешнее и внутреннее давление. Резак испытывали непрерывно в течение одного часа при 110 об/мин и 20 бар. Масло было слито и проверено после испытания, и никаких признаков проникновения воды не наблюдалось.
Ожидается, что резцы с компенсацией давления для проекта ремонта акведука в Делавэре начнут работу в конце декабря 2017 года, а первые результаты будут представлены на конференции.
4. СИСТЕМА КОНТРОЛЯ ФРЕЗЫ
Компания Robbins разработала и использовала систему контроля резцов на нескольких проектах по разработке твердых горных пород за последнее десятилетие, а за последний год разработала систему нового поколения, известную как SmartCutter. При проходке тоннелей в твердых породах необходима постоянная информация от режущей головки. Конечными целями контрольно-измерительных приборов резака являются мониторинг в режиме реального времени работы отдельного резака, получение более реалистичные значения силы тяги режущей головки и получить более полное представление о геологии перед режущей головкой. Анализ этой информации может дать более глубокие знания о земляных работах. Информация о работе фрезы имеет прямые и косвенные преимущества: она помогает лучше прогнозировать и контролировать интенсивность использования фрезы, а также может снизить стоимость незапланированной замены фрезы или кольца, что может привести к лучшему планированию запасов, рабочей силы и потребности в ремонте фрезы. Еще одним достоинством инструментов для резки является поддержание работоспособности сборки за счет контроля работы отдельной фрезы. Система контрольно-измерительных приборов может уведомлять оператора о неравномерном или сильном износе колец и позволяет предотвратить ненужные замены уплотнений или подшипников. Кроме того, это может предотвратить повреждение режущей головки, вызванное поздней заменой режущей кромки.
Результаты недавних проектов очень многообещающие и предоставляют очень точную и ценную информацию. Система последнего поколения в настоящее время устанавливается на все позиции резцов в рамках проекта ремонта акведука в Делавэре.
4.1.Опыт работы: мониторинг режущего диска на ТБМ AMR Double Shield Hard Rock
Машина AMR представляет собой ТБМ с двойным щитом, работающую в Индии, с диаметром режущей головки 10,0 м и 69 позициями резцов. Во время испытаний нового поколения датчиков контроля фрезы в июле, августе и сентябре 2016 года во время работы контролировалось положение нескольких фрез. Расположение этих резцов изменилось с раб
очей зоны на торцевую, поскольку резцы были перемещены внутрь в положения, где допустимый износ резцов больше.
На рис. 8 показана схема системы AMR SmartCutter. Каждая приборная коробка устанавливалась на клиновой болт корпуса фрезы. На конструкции машинного конвейера установлены два шлюза. Два шлюза обеспечивали постоянную связь. В случае потери связи оператор оповещался на мониторе красной тревогой. Емкость аккумуляторной батареи была увеличена сверх нормального срока службы фрезы, а это означает, что инструментарий может работать в течение одной или нескольких замен фрезы. Кроме того, емкость и состояние батареи постоянно сообщались и отображались на каждом приборе на экране оператора.
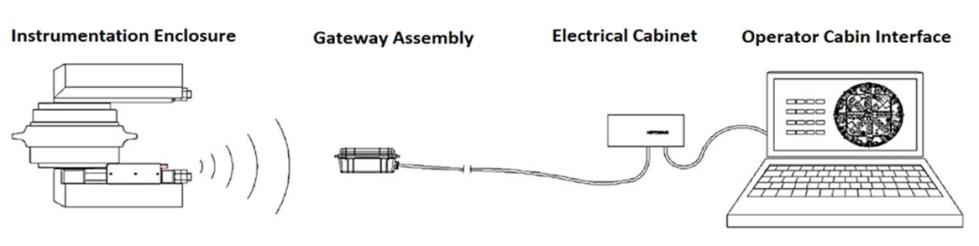
Рисунок 8. Схема системы.
|
Магнитный датчик внутри корпуса прибора измеряет время каждого оборота фрезы в миллисекундах и сообщает скорость фрезы. Зная радиус дисковой фрезы, расстояние фрезы от центральной линии режущей головки, а также скорость режущей головки, можно определить скорость резца. Теперь, используя ту же зависимость и зная радиус и скорость резца, можно рассчитать его износ. Определение разумной скорости выборки и скорости передачи радиоданных имеет решающее значение для получения значимых данных. В то же время для репрезентативного и точного расчета износа требуется детальный алгоритм фильтрации данных.
На рис. 9 показаны восемь минут нефильтрованных данных для одного резака. Из этого рисунка можно определить, что самая высокая скорость, для которой имеется большинство данных, представляет собой нормальную скорость, с которой фреза вращается без перерыва. Если есть какие-либо сбои, когда происходит меньшее, чем истинное качание, следует ожидать снижения скорости. Износ фрезы рассчитывается по известным факторам и отображается на графике на красной линии. Скорость фрезы идеально коррелирует с изменениями скорости фрезы на каждом шаге между 9:59 и 10:01, как и ожидалось.
На рисунках 10A-B ниже показаны результаты износа пяти резцов SmartCutter после фильтрации. На этих графиках также отображается перемещение фрезы. Этот макроанализ показывает очень тесную корреляцию средних значений износа SmartCutter и фактических полевых измерений на фрезах, особенно в пределах ярко выраженного увеличения износа. Операторы могут установить определенные пределы износа для каждой фрезы в настройках предупреждений программы. Во многих случаях предупреждения могут предотвратить дальнейшее повреждение подшипников и ступиц неожиданными проблемами, связанными с износом режущих колец.
5. РАЗРАБОТКА НОВЫХ КОНСТРУКЦИЙ РЕЗЦОВ
5.1. Зажимной дисковый резак
Приведенный ниже узел резака, рис. 11, отличается от обычного резака по двум основным параметрам. Во-первых, диск механически прижимается к ступице, а не приваривается к ступице с помощью приварного стопорного кольца. Во-вторых, диск намного легче (уже), чем традиционный диск.
Такая конструкция позволяет быстро менять диск во время технического обслуживания. Вес диска составляет менее 50% от веса традиционного диска того же внешнего диаметра.
Большая часть всего материала диска приходится на расходуемый изнашиваемый материал. Из-за этого более дорогие материалы дисков становятся практичными. Можно использовать большую часть фрезы, прежде чем ее нужно будет заменить, что обеспечивает экономичный способ проходки туннелей большой протяженности или туннелей, где ожидается высокий износ.
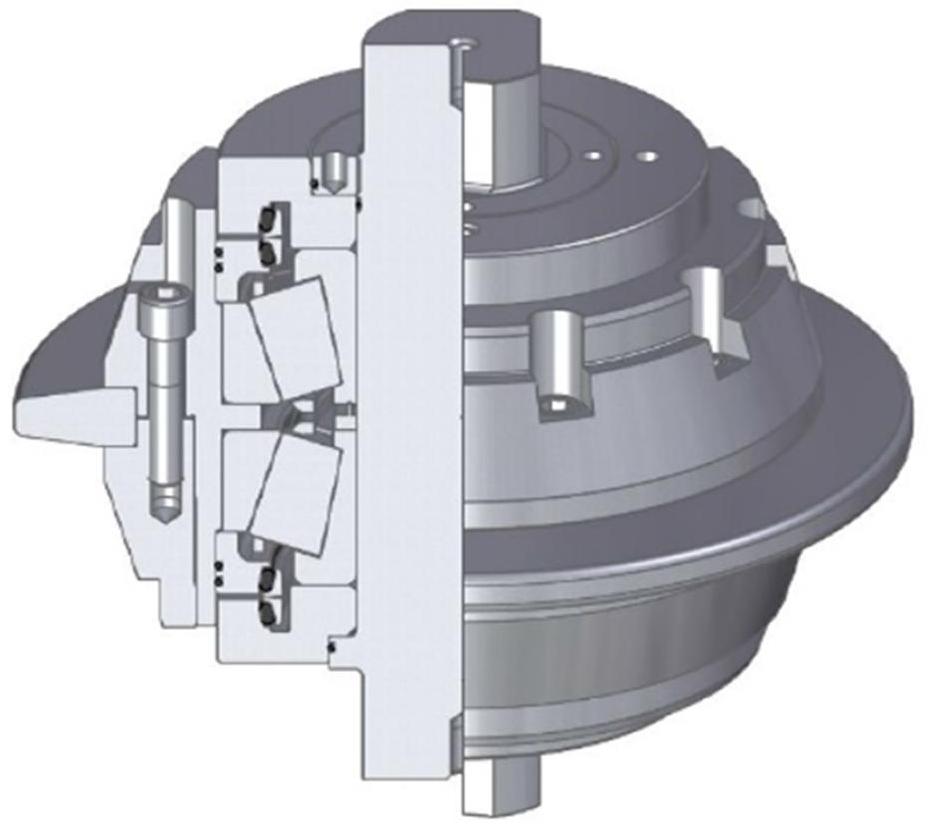
Рис. 9. Принципиальный чертеж фрезы с зажимным диском.
17-дюймовая версия этого нового дизайна проходит испытания с многообещающими результатами. 20-дюймовая версия будет протестирована в начале 2018 года.
5.2. Дисковые фрезы контроля тяги
Этот специальный диск, показанный на рис. 12, был разработан для использования в условиях смешанного или мягкого грунта в твердых породах. Когда ТБМ сталкивается с мягкими грунтами с установленными стандартными дисками из твердой породы, существует вероятность того, что трение между диском и грунтом будет недостаточным для вращения фрезы. Когда фреза не вращается, она со временем изнашивается с одной стороны. Это может произойти быстро, если земля несколько абразивная.
Конструкция фрезы Traction Control сочетает в себе стандартный профиль диска для твердых пород с выступами на боковой поверхности диска, похожими на «фрезу», что дает возможность проникать в почву и заставлять фрезу вращаться.
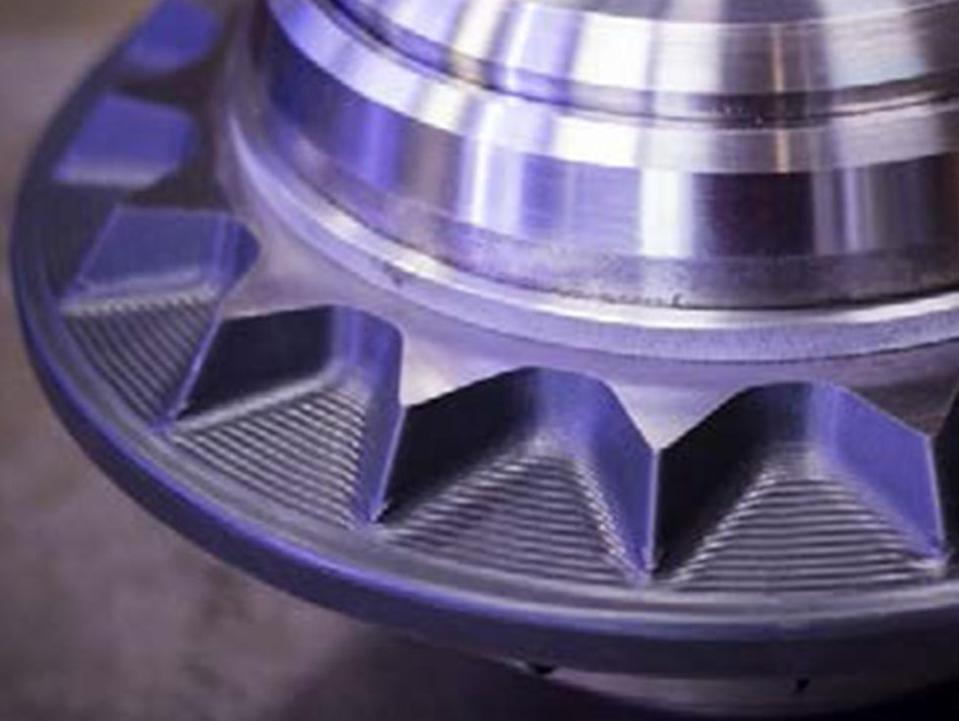
Рис. 10. Изображение кольца диска Traction Control.
6. ЗАКЛЮЧЕНИЕ
Последние технологические разработки, подробно описанные в этом документе, предлагают хорошие возможности для оптимизации срока службы резцов и производительности ТБМ в проектах в условиях твердых пород. Для успешного использования требуется тщательный анализ условий и того, являются ли эти разработки оптимальными, но в проектах с особенно сложным грунтом они могут иметь решающее значение.
Подрядчики должны тщательно взвесить, принесет ли использование дисков большего размера экономическую выгоду. Выбор 20-дюймовых фрез по сравнению с 19-дюймовыми в сочетании с хорошо разработанной программой управления режущей головкой может увеличить время между заменами фрез и увеличить общий срок службы между ремонтами.
Подрядчикам также будет полезно тщательно изучить технологию, применяемую каждым производителем в своих дисковых фрезах. Любой компетентный производитель может изготовить дисковый резак, но доказательство качества диска не будет очевидным, пока сталь не соприкоснется с камнем. Почти все производители дисковых фрез в настоящее время предлагают дисковое кольцо из инструментальной стали, и большинство из них имеют аналогичный состав. Однако разница в производительности определяется не составом кольца диска, а последующей обработкой. Менее дорогие дисковые фрезы не будут экономичными при работе с твердыми породами, если учитывать общую стоимость в течение всего проекта, и это становится все более и более важным по мере того, как порода становится все более сложной.
Хорошо продуманная стратегия резцов наряду с новейшими инструментами высокого качества и инструментальными сталями, разработанными для оптимизации срока службы резцов, может оказать огромное влияние не только на стоимость резцов, но и на производительность ТБМ и общий график проекта.
|
Весь комплекс генподрядных работ по строительству подземных сетей.
. // . ..................................................................... .ceo@микротоннелирование.рф
ПРОЕКТИРОВАНИЕ - ЭКСПЕРТИЗА - СТРОИТЕЛЬСТВО
Благодаря руководству, слаженным усилиям опытных проходчиков, шахтёров и ИТР сложные проекты реализуются качественно и точно в срок.
|