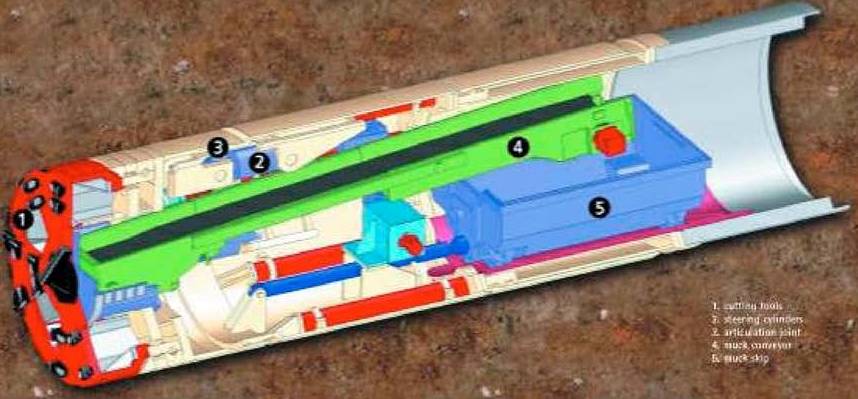
Рис. : Продольное сечение щита TBM 1200.
Подписи к рис.:
1. Рабочий орган
2. управляющие цилиндры
3. шарнир системы управления
4. транспортерная лента для разработанной породы
5. вагонетка для разработанной породы
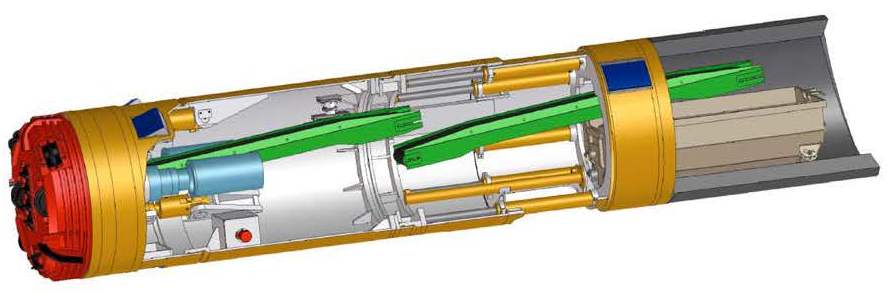
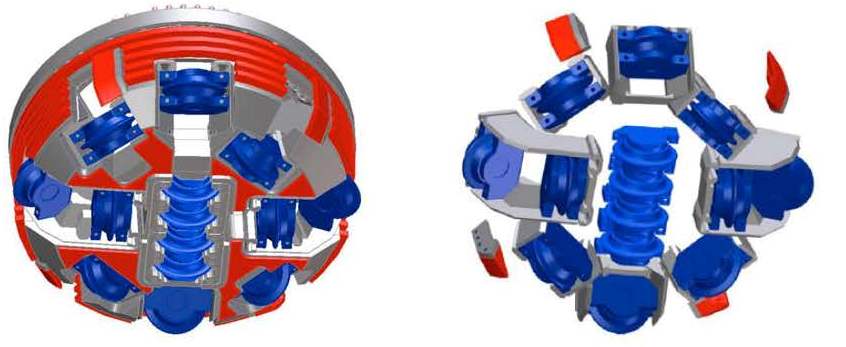
Рис. : Новые разработки в рабочем органе щита TBM 1200002E
- Режущие диски (шарошки) диаметром 280 мм устанавливаются на подшипниках по одному, это позволяет добиться на 32% более высокого усилия прессования
- В общей сложности используется 14 одинарных дисков вместо прежних 10 одинарных и двойных дисков (шарошек)
- Рабочий орган выпуклой формы имеет большую площадь для размещения шарошек
- Система Backloading (способ крепления инструмента, позволяющий заменять режущий инструмент без выхода за ротор в призабойную зону)
- Может оснащаться грипперами
- Для крепления центральных дисков (шарошек) используется усиленная система крепления
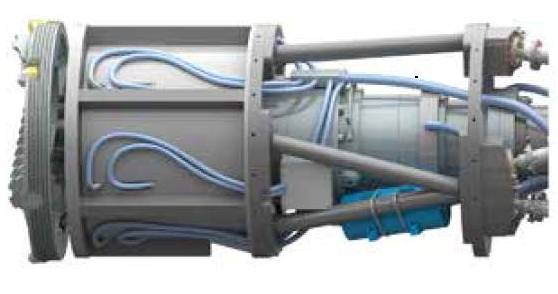
Рис. Система эрозии почвы с пульпопроводами
Дизайн и конструкция машины состоит из пяти важных подразделов, в каждом из которых есть свои тонкие, а некоторые и существенные инновации.
Режущая головка состоит из вращающейся головки, оснащенной дисками для измельчения твердой почвы и конусной дробилки.
Этот коническая конусная дробилка состоит из нескольких стальных колец с покрытием из карбида вольфрама и может дробить породу на мелкие кусочки размером 1-2 см, чтобы их можно было транспортировать по пульпопроводу к выходу из туннеля. Покрытие из карбида вольфрама обеспечивает долговечность и позволяет дробилке лучше захватывать камни.
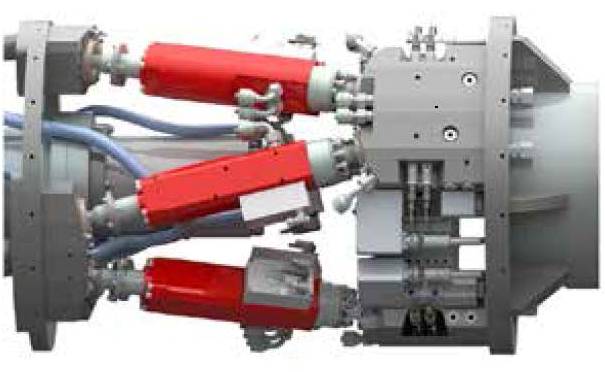
Рис. Шесть высокоточных гидравлических цилиндров позволяют режущей головке
перемещаться по всем шести степеням свободы.
«Грунтовая жижа вымывается из эрозионная камера с использованием давления воды 10 бар и струйного насоса, расположенного в задней части машина. Насос использует эффект Вентури создать вакуум и высасывает разрушенный грунтовой материал перемещается через машину к выходу из туннеля, — объясняет, — с крутящим моментом 8,5 кНм, скоростью вращения 27 об/мин и усилием толкания 200 кН мы чувствовали себя готовыми к любым условиям мягкого грунта, которые мог выдержать машина».
Чтобы управлять машиной во время бурения и позволять ей двигаться по криволинейным траекториям, была внедрена и интегрирована в ТБМ инновационная гидравлическая шестигранная система, которая называется платформой Стюарта.
Спасибо шести высокоточным гидравлическим цилиндрам можно перемещать режущую головку по всем шести степеням свободы. «Кроме того, специальное программное обеспечение, разработанное в сотрудничестве с одним отраслевым партнером, позволяет переводить систему в так называемый режим отбойного молотка, который допускает вибрации.
индуцироваться частотами до 20 Гц,
«Вибрируя с такими высокими частотами, режущая головка могла бы освободиться, если бы она застряла в земле».
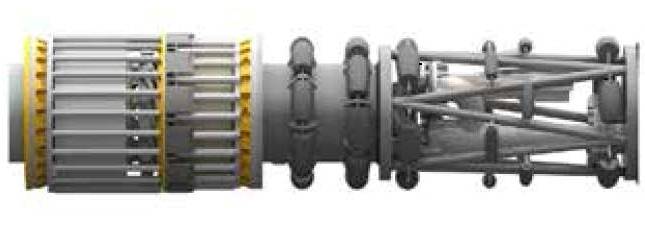
Рис. Инновационная система футеровки, напечатанная на 3D-принтере.
Однако одной из наиболее впечатляющих конструктивных особенностей является система облицовки туннеля, разработанная SLT. Гениально это позволяет непрерывное строительство туннеля «футеровки» вокруг машины с использованием уникального полимерного 3D-принтера, встроенного в машину. Благодаря применению прочных ламелей из стекловолокна и двухкомпонентной полимерной смеси ММА, экструдированной через специально разработанные сопла, можно создать высокопрочную тоннельную обделку толщиной 15 мм, обеспечивающую структурную целостность по всей длине тоннеля. На заключительном этапе также разворачивается внутренний слой пластикового листа, чтобы полимер не капал внутрь машины.
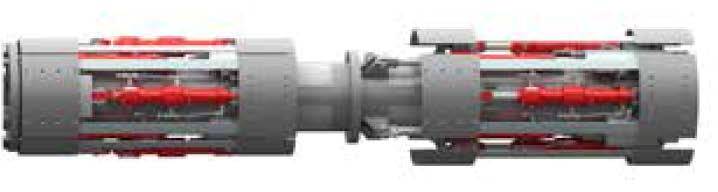
Рис. Силовая установка с высокопроизводительными гидроцилиндрами,
размещенными на двух одинаковых секциях.
Этот подход делает проходку туннелей более эффективной, поскольку он позволяет машине непрерывно копать и передавать тяговое усилие непосредственно через конструкции туннеля, построенные на борту. 3D-принтер также позволяет футеровку криволинейных туннелей, что делает ТБМ более маневренным, чем обычные системы проходки туннелей, особенно работая в тандеме с ранее описанной системой наведения.
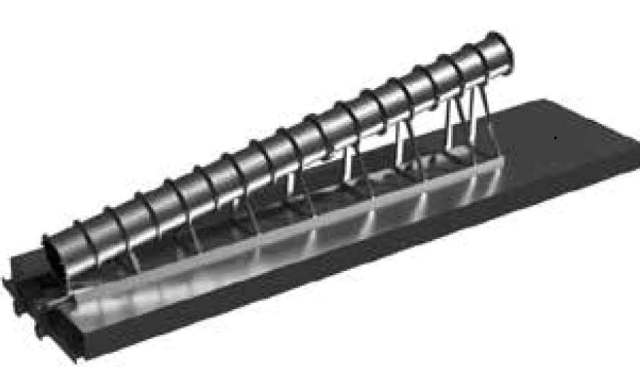
Рис. Стартовая платформа
Чтобы продвигать ТБМ вперед со стартовой платформы через туннель, инженеры SLT спроектировали, изготовили, собрали и испытали силовую установку с гидравлическим приводом. Он состоит из 16 скоординированных высокопроизводительных гидравлических цилиндров, расположенных на двух одинаковых секциях. Восемь
используются для прижатия так называемых силовых распорок к конструкции туннеля, выдавливаемой описанной выше системой туннельной облицовки, в то время как остальные восемь
отвечают за толкание машины вперед с максимальным усилием 200 кН. Движение обеспечивают подшипники скольжения, расположенные на контактной поверхности между внутренней рамой машины и распорными трубками, к которым прикреплены цилиндры.
|