Выдержка:
Слиманабадский транспортный канал в Индии является ярким примером того, насколько сложным могут быть смешанные состояния грунта, хотя существуют и другие примеры. Тоннель перекачки воды находится в стадии строительства. бурение с использованием гибридного ТБМ типа скала/EPB диаметром 10 м. Однако за 6,5 лет проходки туннеля
машина продвинулась всего на 1600 м. Коммерческие проблемы первоначального подрядчика застопорили проект часто, а наземные условия оказались еще более сложными, чем предполагалось. Низкий вскрышных пород от 10 до 14 м в сочетании со смешанными забоями, переходными зонами и высокий уровень грунтовых вод ограничивал темпы продвижения. Производитель ТБМ мобилизовал команду для ремонта TBM, и в течение 6 недель была развернута команда из 180 человек, чтобы взять на себя все аспекты туннелирования и поддержки деятельности. Производительность резко возросла, когда ТБМ за четыре месяца продвинулся более чем на 400 м. В этой статье будут обсуждаться проблемы, с которыми столкнулись, и методология, которая обеспечила хорошую скорость проходки в сильно изменчивых условиях смешанного забоя.
1. ВВЕДЕНИЕ
Проект отвода Барги в Мадхья-Прадеше, Индия, представляет собой ирригационный проект через долину, состоящий из 197 километров канала. Он будет перекачивать воду из реки Нармада для обеспечения орошение 245 000 га земли в подверженных засухе районах в Сатне, Джабалпуре, Катни и Районы Ревы. Он также будет поставлять 284 миллиона литров бытовой и технической воды в день. город Джабалпур и город Катни. Участок схемы включает в себя 12-километровую туннель проходимый гибридной ТБМ Роббинс диаметром 10,0 м: порода/ЭПБ.
2 ГЕОТЕХНИЧЕСКИЕ УСЛОВИЯ
Геология вдоль трассы туннеля часто меняется. Состоит из плотных остаточных грунтов,
алевриты, аллювий, сильно выветренные известняки и доломиты, с прослоями сланца, массивные кристаллические известняк и свежий мрамор. Прочность породы значительно зависит от значений UCS. достигает 180 МПа. Имеется высокопроницаемый валунный горизонт, который действует как канал для грунтовых вод, расположенных на 2-3 м выше тоннеля на начальных 2,7 км трассы. уровень грунтовых вод находится над тоннелем по всей длине проезда. В некоторых случаях ТПМ преодолела переходные зоны между различными геологическими условиями в пределах 1-2 метров от бурение, а в других случаях переходная зона простиралась более чем на 100 метров. Эти длинные
переходные зоны приводят к трудным условиям бурения из-за смешанных забоев.
Рисунок 1 - показаны прогнозируемые геологические условия для начальных 3400 м трассы тоннеля.
3 ВЫБОР ТБМ
В геологических отчетах указано, что примерно 68% (8 160 м) туннеля будет
пройденный через остаточные почвы, ил и сильно выветренные / разложившиеся породы, с оставшимися
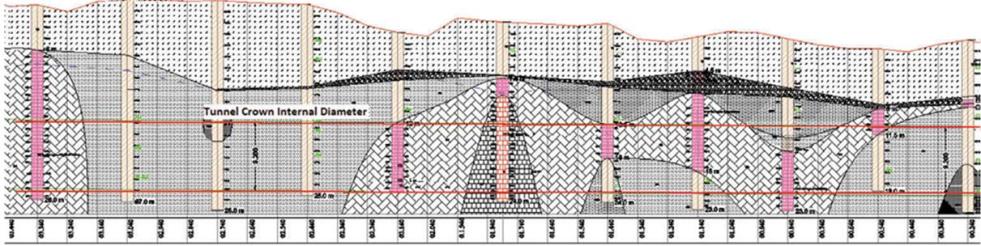
Рисунок 1. Геологическое выравнивание.
32% (3840 м) проходят через прочную скалу. Имея это в виду, гибридный рок/EPB
машина рассматривалась для проекта. Гибридная машина будет настроена с
возможность замены винтового конвейера на ленту ТПМ и взаимозаменяемость
между дисковыми фрезами и инструментами для мягкого грунта (см. рис. 2).
Приблизительно 600 м из предполагаемых 3840 м компетентной породы было разделено на многочисленные, относительно короткие отрезки. Эти короткие отрезки времени не оправдывают месячного простоя. необходимо снять винтовой конвейер, установить ленточный конвейер и перейти с EPB на жесткий режим рок. Однако более 3200 м прочной скалы состояло из трех участков по 700 м. м, 1000 м и 1500 м. Длина этих отрезков гарантировала время простоя, необходимое для преобразования
из режима EPB в режим хард-рока; Поэтому было принято решение использовать гибридную машину для Слиманабадский проект. Основные технические характеристики ТБМ приведены в таблице 1.
4 СБОРКА И ЗАПУСК МАШИНЫ
Машина была собрана на удаленной строительной площадке с использованием технологии первичной сборки на месте (OFTA). метод, который позволяет первоначально собрать машину на месте с тестированием критических узлы в мастерской. ТБМ был запущен в начале марта 2011 года в режиме EPB с полный комплект орудий мягкого грунта, так как геологическая информация указывала в основном на мягкий грунт для
начальные 500 м бурения. На первых 200 м бурения ТБМ столкнулся со смешанной
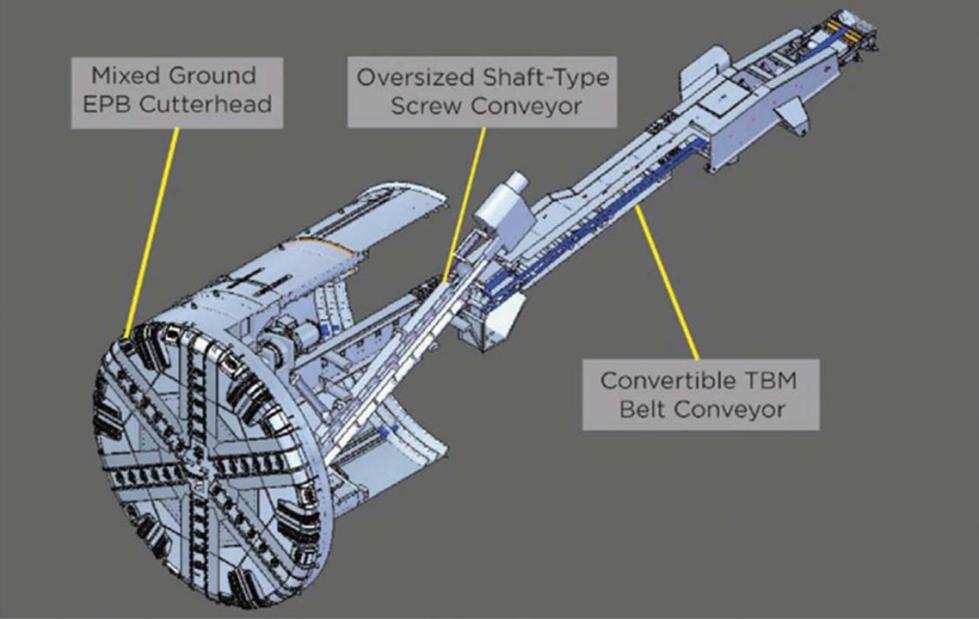
Рисунок 2. Характеристики ТБМ в Слиманабаде
Геологический условия, с которыми пришлось столкнуться во время первых 1600 м бурения. Сила скала потребовала замены инструментов для мягкого грунта дисковыми фрезами. После изменения без режущих инструментов, машина бурила в скале, но все равно должна была работать в закрытом/ Режим EPB для предотвращения оседания грунта над сводом тоннеля (см. рис. 3-4).
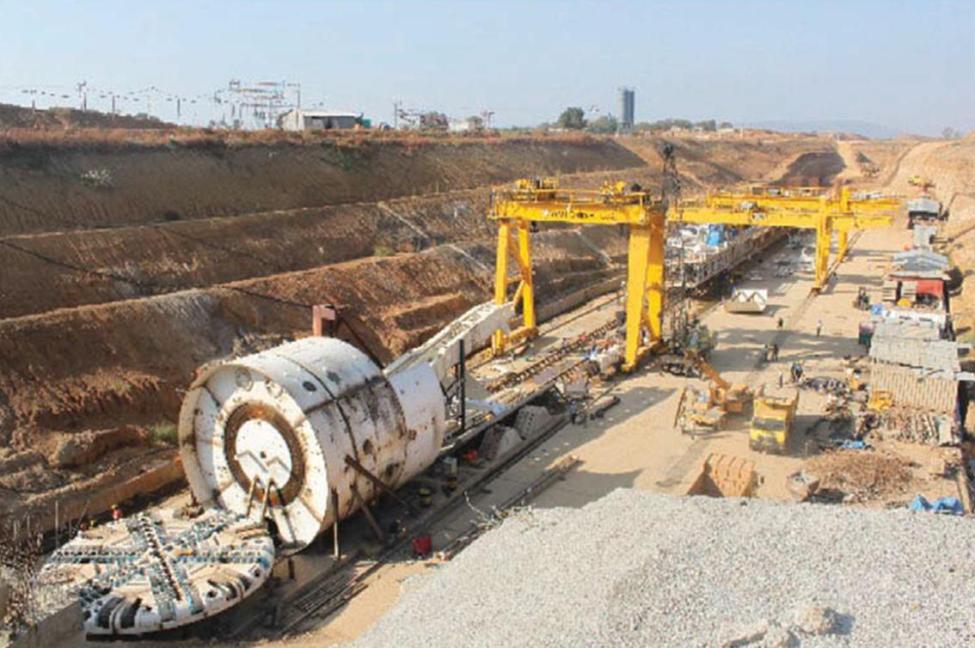
Рисунок 3. Сборка ТБМ на месте.
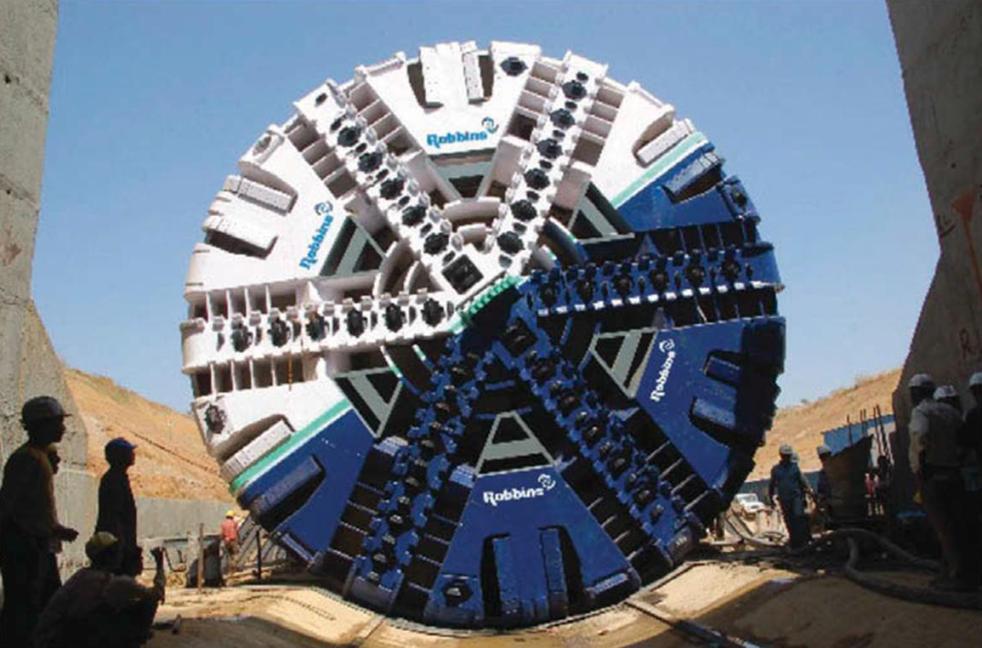
Рисунок 4. Запуск ТБМ. |
5. ИСТОРИЯ ПРОЕКТА ПОСЛЕ ЗАПУСКА
В течение следующих 6,5 лет после запуска машины проект претерпел множество
проблем как коммерческих, так и технических. Полный отчет о коммерческом
проблемы не входят в предмет данной статьи; тем не менее, следует отметить, что они привели к различные незначительные задержки до нескольких недель из-за нехватки запасных частей, сегментов и расходных материалов и т. д. Они также привели к полной остановке проекта в двух разных случаях. на десять месяцев и восемь месяцев соответственно. Основные технические проблемы, с которыми сталкивается проект
столкнулись, подробно описаны ниже.
5.1 Неудачное вмешательство режущей головки
Во многих случаях операции с режущей головкой в ??гипербарических условиях должны были быть либо отменены до того, как они могли начаться, или были прерваны во время выполнения из-за чрезмерного количества воздуха потери. Критически длительное время вмешательства может привести к эрозионным выбросам. Мелкие частицы почвы являются выдувается из земли, увеличивая размер пор и уменьшая сопротивление потоку воздуха (Бабендерерде и др., 2014). На проекте Слиманабад причиной потерь воздуха была просачивание воздуха. через проницаемый материал над венчиком туннеля, особенно через валунный горизонт. Проблема усугублялась низкой вскрышной породой всего 10-14 м. стандартная практика введения бентонита в лицо для образования корки, чтобы предотвратить или, по крайней мере, минимизация потерь воздуха оказалась безуспешной, так как бентонит выталкивался на поверхность вместе с выходящим воздухом. В связи с неудачей закачки бентонита было принято решение установить безопасные цементные блоки через бурение и закачка с поверхности. Первоначально это решение оказалось ненадежным, так как 5.2 Повреждение режущей головки.
Из-за отсутствия своевременных вмешательств в режущую головку режущая головка пострадала от износа. степени, которые требовали ремонта в трех отдельных случаях. Из-за малой перегруженности и смешанные геологические условия, было решено, что выемка грунта с поверхности вниз до TBM было бы намного проще, чем создание подземной камеры для проведения ремонта. Ни один ни сегментов ствола, ни сваебойной техники на площадке не было, но тяжелая землеройная техника
использовался на работах на канале. Наличие этого оборудования позволило
создать выемку карьерного типа (см. рис. 5). Остаточные грунты и аллювиальный материал было относительно легко выкопать, но их низкая связность потребовал многоуровневого котлована с несколькими уступами и потребовал выемки около 30 000 м?. материала. Одной из проблем, с которыми пришлось столкнуться при проходке карьеров, было разжижение, вызванное насыщением грунта и вибрацией землеройной техники (см. рис. 6).
Три отдельные операции по ремонту режущей головки, включая выемку грунта и обратную засыпку. карьеров, что привело к общей задержке более чем на восемь месяцев. 5.3 Разлив навоза При растачивании в режиме EPB важно, чтобы в шнеке образовалась пробка из материала, поддерживать лицевое давление. Для формирования пробки требуется достаточное количество мелких частиц в
раскопанного материала. В створе тоннеля до высоты 1600 м было проложено более 300 м 3608 нехватка специализированных подрядчиков в регионе и субподрядчика, нанятого для выполнения работ не хватало необходимого опыта и оборудования. Первая попытка протолкнуть ТБМ в предварительно установленный блок цементного раствора для проведения вмешательства режущей головки под давлением полностью вышел из строя
из-за чрезмерной потери воздуха. Это вызвало задержку примерно на одну неделю во время ожидания второго цементный блок должен быть установлен в 10 метрах от машины. К сожалению, после скучного вперед во второй цементный блок, вторая попытка вмешательства также не удалась из-за избыточного воздуха потери. Качество и эффективность безопасных цементных блоков со временем улучшились, но они
никогда не были близки к 100% эффективности и были причиной многих дальнейших задержек.
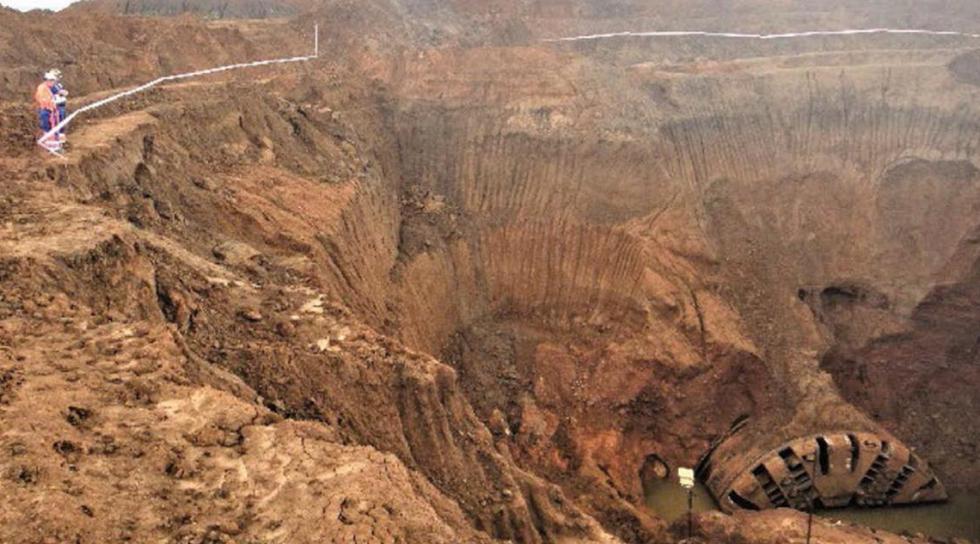
Рисунок 5. Выемка грунта до ТБМ.
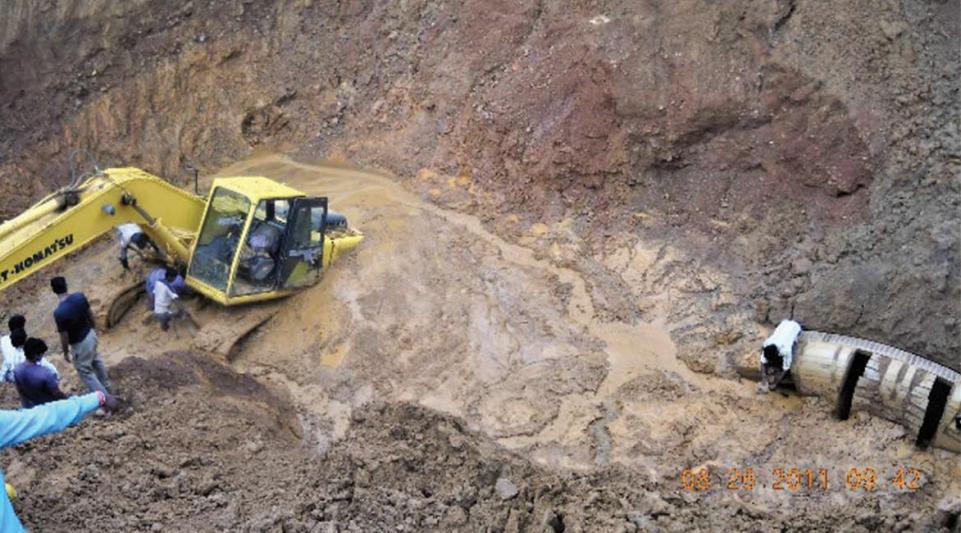
Рис. 6. Разжижение грунтов.
сильно выветрелый или умеренно выветрелый мрамор и сланец и 200 м смешанных условий забоя при отсутствии достаточного количества штрафов. Отсутствие штрафов при
высокий уровень грунтовых вод и проницаемая геология вызвали проблемы с поддержанием забойного давления. Этот привело к относительно распространенной проблеме для EPB в этом типе геологии: вода под высоким давлением и высыпание ила из точки передачи между винтовым конвейером и ленточным конвейером ТПМ.
Водосборная коробка и насос были доступны на месте (как часть конструкции и поставки машины). но количество разливов значительно превышало его вместимость. Полимеры и бентонит были закачаны в забой тоннеля, пленум и винтовой конвейер, но они имели минимальный эффект из-за чрезмерного объем воды. Задержки с ручным устранением разлива составили почти 80% рабочее время. Обычно ход бурения длиной 1,6 м выполняется менее чем за два часа, но оставшаяся часть 10-часовой производственной смены будет посвящена устранению разливов.
5.4 Воронки
Проблема, связанная с неудачным вмешательством режущей головки, заключалась в появлении воронок над машине (см. рис. 7). Несколько вмешательств были прерваны в течение 48 часов после их начала. из-за постепенного увеличения потерь воздуха. Стандартной практикой стало снижение гипербарического давления. до минимума (около 0,9 бар), чтобы уменьшить количество потерь воздуха; следовательно, это также расширило продолжительность вмешательства. Однако иногда это приводило к постоянному промыванию водой. мелкие частицы и ил в камеру режущей головки и вокруг внешних щитков ТБМ. Диаметр отверстия режущей головки с новыми резцами составляет 10,0 м, а наружный диаметр щитов ТБМ составляет 9,93 м (дифференциал необходим для рулевого управления и входит в стандартную комплектацию
дизайнерская практика). Общая длина щитов ТБМ составляет 11,2 м, что соответствует 12,3 м?. кольцевого пространства вокруг щитов. При сохранении достаточного давления на лицо риск конвергенция сведена к минимуму, но снижение давления позволило добиться конвергенции. Комбинация
поступления мелочи в камеру и схождения вокруг кольцевого зазора привели к
полости, образующиеся над режущей головкой и щитками и в конечном итоге выходящие на поверхность. Провалы обычно возникали после того, как машина продвинулась на 2-3 кольца после вмешательства. было завершено. Участок, где образовались воронки, является частью 95% выравнивание туннеля, которое проходит под сельскохозяйственными угодьями, поэтому не было риска для поверхностных сооружений. Доступ к земле через первые 1,5 км туннеля был относительно простым,
поэтому для засыпки воронок была задействована землеройная техника. Обычно после менее чем 24 часа скучно было в состоянии продолжить.
6 ПРИВЛЕЧЕНИЕ ПОСТАВЩИКА ТБМ
Первоначальное участие компании Robbins в проекте Слиманабад заключалось в поставке и ввести в эксплуатацию ТБМ и туннельные конвейерные системы, а затем предоставить ключевой персонал для обучения бригад подрядчика и устранение технических неполадок с оборудованием. В сентябре 2017 года, после того, как за 6,5 лет было завершено всего 1600 м туннеля, проект владелец и старший партнер по совместному предприятию провели переговоры с The Robbins Company с целью берется за проект. Хотя Роббинс не имел постоянного присутствия на объекте во время предыдущие 6,5 лет они были вовлечены в проект в различных качествах с тех пор, как запуск машины. Из-за этого участия они были знакомы с трудностями проект столкнулся, и они приняли вызов. Новый объем работ Роббинса охватывал все аспекты производственных операций, включая туннельные и наземные работы, поставку рельсов, труб, кабели, расходные материалы, цементный раствор, электричество и вывоз выкопанного материала с площадки. Поставка
сегменты остались в сфере деятельности старшего партнера по СП. Была мобилизована бригада для начала ремонта. и испытания ТБМ в сентябре 2018 г. К концу октября 2018 г. размер команда была увеличена до 180 человек, чтобы обеспечить начало производственных операций.
7 ПЕРЕЗАПУСК ПРОЕКТА
Тщательный анализ причин задержек с целью повышения производительности.
сталкивался до тех пор, пока этот пункт не был выполнен. Меры, принимаемые для смягчения этих проблем, перечислено ниже.
7.1 Уменьшение потерь воздуха во время вмешательств
Общая эффективность и результативность вмешательств с ножевыми головками сыграли ключевую роль в улучшение общего производства по проекту в Слиманабаде. Исторически сложилось так, что создание убежища цементные блоки с поверхности оказались менее чем эффективными для предотвращения потерь воздуха
во время интервенций. В ходе обсуждений было решено, что закачка жидкого тампонажного раствора изнутри TBM давал больше шансов на успех, так как давление цементного раствора нарастало с лицевой стороны. туннель, способствуя перемещению цементного раствора в разрывы и проницаемые материал над ТБМ. Другой вопрос, который необходимо было рассмотреть, заключался в том, что туннель
выравнивание удалялось от относительно легкодоступных точек на поверхности. Это означало, что транспортировка бурового и насосного оборудования в места над тоннелем
стать намного сложнее. В течение следующих трех вмешательств слабая смесь
цементный раствор прокачивался через смесительную камеру ТБМ в окружающую геологическую среду.
В каждом случае потери воздуха были сведены к минимуму, а вмешательства проводились без Основные проблемы. Состав цементной смеси был изменен при каждом из этих трех мероприятий. Окончательный вариант дизайна можно увидеть в таблице 2.
Вместо того, чтобы устанавливать ограничение на фактический объем раствора, который должен быть закачан в землю, нарастание давления цементного раствора использовалось для определения того, когда было закачано достаточное количество цементного раствора. Используемый контрольный показатель был на 0,3 бар выше давления EPB, используемого во время бурения. Когда-то это давление было достигнуто, откачка была остановлена ??на 15-20 минут, чтобы определить, является ли зарегистрированное давление произведение противодавления во время откачки. Если давление упало более чем на 0,2 бар в течение Через 20 минут возобновляется заливка цементным раствором до тех пор, пока не будет достигнуто установившееся давление.
7.2 Время, затрачиваемое на метод заливки слабой смесью
Время схватывания слабой смеси составляет от 12 до 18 часов в зависимости от таких переменных, как количество закачанного раствора, количество грунтовых вод, температура и т. д. Время, затраченное на перекачивать слабую смесь также необходимо учитывать при расчете общего времени. Дополнительное время также необходимо учитывать при очистке ножевого вала и замене ножей. Это, конечно, результат необходимости удаления цементного раствора, а не просто очистки почвы от спиц режущей головки, ведра и фрезы. Как правило, на общее вмешательство в режущую головку ушло около 20 часов. график при использовании жидкого цементного раствора для укрепления грунта. Это должно быть записано что 20 часов следует использовать в общем графике только тогда, когда принимается решение прокачивать слабую смесь
затирка берется до начала вмешательства. В этот момент смесительная камера
упакован выкопанным материалом и температура этого материала выше, чем температура окружающей среды температура на ТБМ. Камера, заполненная навозом, сводит к минимуму количество требуется слабая смесь, а более высокая температура сокращает время ее схватывания. После проведения нескольких успешных вмешательств с использованием метода слабой смеси, TBM столкнулся с полным лицом остаточной почвы. Попытка вмешательства без откачки слабый цементный раствор, и это оказалось успешным. К сожалению, последующее вмешательство в очень похожие наземные условия пришлось прервать из-за чрезмерных потерь воздуха. Для того, чтобы
уменьшите потери воздуха и завершите это вмешательство, перекачивая слабый цементный раствор из снова была использована ТБМ; однако добавление слабой цементной смеси в этот момент добавило дополнительные 18 часов к стандартным 20 часам, связанным с использованием методологии слабой смеси.
Это связано с тем, что камера во время вмешательства более чем наполовину пуста, поэтому время требуется перекачать дополнительно 40 + м? слабой смеси для замены вынутого материала. Дополнительный время схватывания требуется для дополнительного раствора и для очистки режущей головки и ножей
так как в ножевой головке меньше почвы, чтобы раствор не прилипал к спицам ножевой головки, ковшам и режущие инструменты. В Слиманабаде нет четких правил относительно того, следует ли качать слабый цементный раствор.
смесь перед вмешательством, потому что геология менялась слишком часто для твердых и быстрые правила. Решение было принято на основе наблюдательного подхода; тем не менее, первостепенное значение
Философия была такова: «если сомневаетесь, закачивайте жидкий цементный раствор». В долгосрочной перспективе эта философия значительно сократил общее среднее время, затрачиваемое на каждое вмешательство, за счет уменьшения количества вмешательства, которые необходимо было прекратить. Это также полностью отменило необходимость установки сейфа. убежище затирки блоков с поверхности.
8 ПОВРЕЖДЕНИЕ РЕЖУЩЕГО ИНСТРУМЕНТА И РЕЖУЩЕЙ ГОЛОВКИ
Сокращение количества смен фрезы автоматически сокращает время простоя.
для вмешательств с режущей головкой и впоследствии повышает общую производительность. Это было случай в Слиманабаде, где замена шести катеров при гипербарических вмешательствах могла занять более девяти часов. Это не считая времени, затрачиваемого на очистку и осмотр режущей головки. и режущие инструменты, что занимает примерно шесть часов в дополнение к 20 часам, связанным с
с перекачиванием слабой тампонажной смеси. Общее время вмешательства для замены шести резцов составило не менее 35 часов, что соответствует почти шести часам на резак.
Очень важно как можно скорее выявить отдельные поврежденные фрезы. Когда один резак получает блокируется и перестает вращаться, это приводит к более высокой нагрузке на соседние фрезы с возможностью каскадный отказ (удаление) всех резаков в худшем случае (Shanahan 2010). Каскадные вайпауты может привести к повреждению ножевого вала, и повреждение может произойти в процессе скучно всего пару штрихов. Проблема со смешанной выемкой забоев постоянно меняется. геология заключается в том, что предсказать закономерности износа фрез чрезвычайно сложно. Более того, пара
поврежденные резцы не оказывают существенного влияния на наблюдаемые рабочие параметры Машина диаметром 10,0 м работает с тягой 24 000 кН и режущей головкой 12 000 кНм. крутящий момент. Чтобы повысить вероятность обнаружения любых изменений в параметрах, Роббинс развернул самых опытных операторов, которые были доступны для этого проекта. Кроме того, политика проведения вмешательство, если наблюдалась какая-либо аномалия в параметрах бурения. Еще одним важным фактором снижения расхода фрезы была минимизация повреждений от ударов. к режущим дискам в геологии смешанных забоев. Ударное повреждение возникает, когда режущие диски
вращение через относительно мягкий материал перед контактом с более твердым материалом, что может привести к образованию радиальных трещин в режущих дисках и отрыву дисков от
концентраторы. Величина удара зависит от скорости вращения режущей головки и
глубина проникновения за один оборот. Чем выше процент мягкого материала в смешанной геологии,
тем выше риск повреждения режущих дисков.
Чем ближе фреза к периферии ножевого вала, тем выше риск повреждения.
Ограничение скорости перемещения фрезы является наиболее важным фактором во избежание повреждения при ударе и Эмпирическое правило, используемое в Слиманабаде, заключалось в том, что максимальная скорость движения фрезы составляла 30 м/мин. Если мы рассмотрим что калибровочные фрезы на режущей головке диаметром 10,0 м проходят расстояние 131,42 м за оборотов, то 0,95 об/мин определяется как максимальная скорость вращения ножевого вала, чтобы
остаются ниже максимальной скорости перемещения фрезы 30 м/мин в условиях смешанного забоя. Вторым по важности механизмом снижения повреждений при ударе является ограничение глубины проникновения фрезы в точке столкновения между мягким и твердым материалом (см. рис. 8). Опыт проекта Sleemanabad определил, что эта глубина составляет примерно 8 мм.
На рис. 9 показаны два смешанных состояния забоя, типичные для переходных зон, с которыми пришлось столкнуться. вдоль трассы Слиманабадского проекта. В условиях смешанного забоя, показанных на A калибровочные фрезы проходят через мягкий материал под углом 90?, прежде чем вступить в контакт с рок. Если мы посмотрим на скорость проникновения 15 мм/оборот (что достижимо в грунтах и более мягкая порода), проникновение в точке контакта с более твердой геологической структурой выглядит следующим образом:
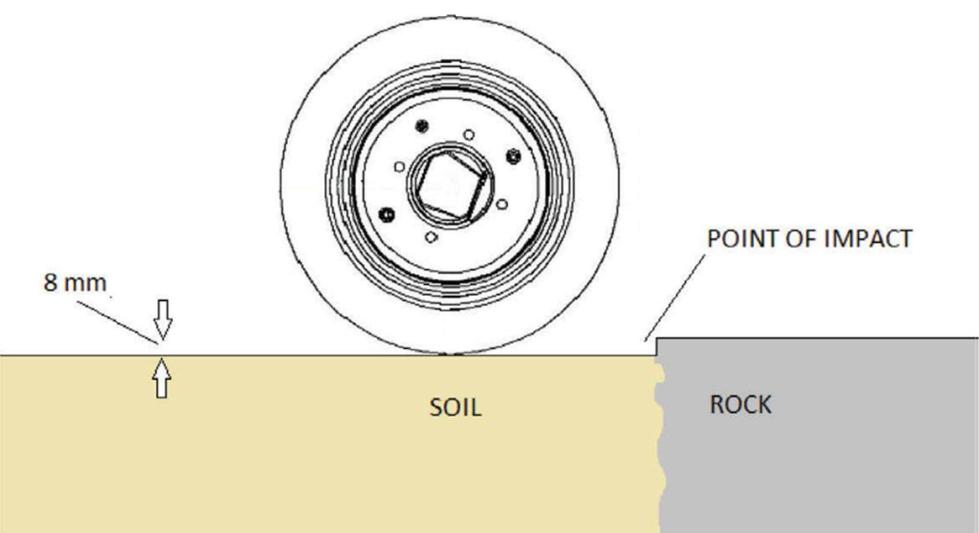
Рис. 8. Ограничение глубины проникновения фрезы в точке соударения между твердым и мягким материалом.
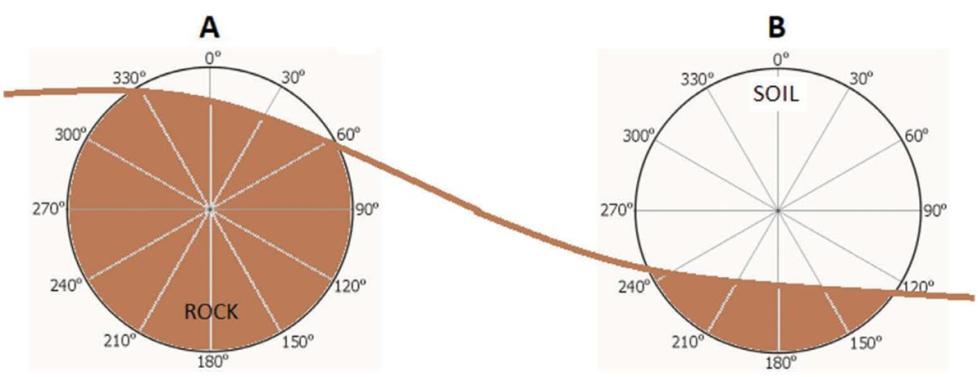
Рис. 9. Два смешанных забоя, типичных для переходных зон Слиманабада.
15 мм/360?*90? = проникновение 3,8 мм в точке контакта с более твердой геологической структурой, что находится в пределах допустимых параметров, установленных на сайте.
В условиях смешанного забоя, показанных на B, калибрующие фрезы прошли бы 240? мягкого забоя. материала до контакта с камнем. При той же скорости проходки 15 мм/оборот проникновение в точке контакта с более твердой геологией выглядит следующим образом: 15 мм/360?*240? = проникновение 10 мм в точке контакта с более твердой геологией, что выходит за допустимые пределы, установленные на сайте. В этом случае давление главной тяги ТПМ будет уменьшено, чтобы уменьшить проникновение за оборот примерно до 12 мм (12 мм/360?*240? = 8 мм).
Картирование лица проводилось во время каждого вмешательства, а пробы навоза брались во время каждый ход, чтобы предоставить наилучшую возможную информацию для обеспечения правильных рабочих параметров можно было идентифицировать. Скачана информация о реальных параметрах растачивания станка из регистратора данных ежедневно, чтобы подтвердить, что назначенные рабочие параметры были соблюдены.
9 РАЗЛИВ ГРЯЗИ
Разлив навоза был наиболее серьезной причиной задержек после неудачных вмешательств с режущей головкой. и повреждение режущей головки. Крупные утечки часто происходили сразу после неудачных вмешательств. или расширенных вмешательств, а также в областях, содержащих недостаточное количество мелких частиц, чтобы удерживать вилку в Рис. 8. Ограничение глубины проникновения фрезы в точке соударения между твердым и мягким материалом. Рис. 9. Два смешанных забоя, типичных для переходных зон Слиманабада.

Рисунок 10. Перекрывающиеся лотковые трубы использовались для отвода разливов в скипы навоза. |
винтовой конвейер. Это связано с тем, что потери воздуха и/или пониженное давление на лице позволили воде попасть в окружающая геология мигрировать в камеру машины. Когда скука возобновилась, эта вода смешивалась с выкопанным материалом и превращала его в кашицеобразную консистенцию, которая привело к значительным утечкам. Как и в случае с участками, содержащими недостаточное количество мелких частиц, закачка полимера в камеру и винтовой конвейер не оказала заметного влияния на
количество разлива. Поскольку объем утечки нельзя было уменьшить, единственным оставшимся решение состояло в том, чтобы потратить определенное количество времени на настройку системы, чтобы поймать утечку, а не чем тратить значительно больше времени на его очистку. Как упоминалось ранее, водосборная коробка и шламовый насос были доступны на объекте, но количество разливов значительно превышало его производительность. В начале хода бурения количество пролива достигало 200 л/мин.
примерно 90% грунтовых вод и 10% смеси ила, мелочи и мелкой каменной крошки.
Примененное решение состояло в том, чтобы закрепить постоянный желоб ниже точки передачи шнека. конвейер/ленточный конвейер TBM. Перед началом каждого прохода бурения было выполнено четыре пропуска грунта. размещается на устройстве подачи сегментов и позади него. Сегментный кран и сегментный питатель использовались для
поместите пропуски в правильные места и удалите их после завершения бурения
Инсульт. Ряд перекрывающихся водосточных труб (половина труб) использовался для направления утечки в скипы (см. рис. 10). Избыток воды стекал по верхним краям
скип, и поскольку каждый скип был заполнен илом / мелкими частицами / каменной крошкой, труба желоба была удалена, чтобы позволить следующий пропуск в очереди, который нужно заполнить. Избыток воды откачивали в отстойник перед
выкачивают из туннеля. Установка скипов для навоза и водосточных труб заняла около 30 минут. Удаление их в конце хода и очистка незначительного разлива заняла примерно 60 минут. Еще 30 минут было потеряно на погрузку кольца на устройство подачи сегментов, потому что навоз проскакивает. располагались на сегментном питателе при растачивании хода. Общая задержка около двух часов на гребок было значительным улучшением по сравнению с восьми часами, которые ранее были потрачены на очистку разливов после каждого удара.
10. УТЕЧКА ЩЕТКИ ИЗ КОЖИ ХВОСТА
Еще одна проблема, которую пришлось решить, когда Роббинс взялся за проект, заключалась в том, что кисточки кожи хвоста были повреждены. Замена поврежденных щеток в геолого-гидрологическом условий, существовавших во время поглощения, необходимо избегать, если это вообще возможно. Это была бы чрезвычайно сложной и трудоемкой операцией с реальным риском потеря земли, что привело к затоплению туннеля водой и илом. Чтобы решить эту был принят подход «назад к основам». Рисовая мякина была получена от местного фермера. который недавно собирал и обмолачивал свой урожай. Четыре мешка (примерно 0,1 м?) половы добавляли в каждую 8 м? порцию цементного раствора. Первоначально можно было увидеть утечку раствора через хвост
кожные щетки, до того, как небольшое количество мякины также наблюдалось, ускользая через щетки.
Количество вытекающей половы постепенно уменьшается до тех пор, пока не произойдет утечка раствора и половы. полностью остановился. Использование мякины будет продолжаться до тех пор, пока машина не войдет в геологическую среду, т.е.
подходит для замены щеток. Предотвращение потери цементного раствора и попадания ила через хвостовик Значительное повышение производительности благодаря очистке от цементного раствора и ила из зоны сборки кольца. и фидер сегмента был серьезной проблемой.
11 ВЫВОДЫ: СОВЕРШЕНСТВОВАНИЕ ПРОИЗВОДСТВА
По проекту Слиманабад потребовалось 6,5 лет, чтобы проложить чуть более 1,6 км туннеля. Даже после вычета почти двух лет остановок из-за коммерческих проблем средняя производительность ставки в оставшиеся 4,5 года составляют менее 30 м в месяц. Улучшения описанные в этой статье, наряду с мобилизацией высококвалифицированного персонала, улучшенный режим технического обслуживания, улучшенное планирование производственной деятельности и улучшенное использование
простоев привело к значительному повышению производительности. В течение первых четырех месяцев после перезапуска было пройдено 400 м бурения. Ни новых технологий, ни дополнительных оборудование было развернуто на объекте. Основная причина улучшения темпы производства определялись опытом и навыками мобилизованной команды. В отрасли это становится все более движимым внедрением новейших доступных технологий важно, чтобы мы не потеряли навыки, которые вырабатывались и передавались из поколения в поколение
тоннельщиков. Новые технологии часто облегчают нашу задачу, но когда операции не облегчают идти по плану, опыт действительно ничто не заменит. |