АБСТРАКТНЫЕ
Есть ли лучший способ построить туннелепроходческую машину (ТБМ), который принесет пользу всем вовлеченным сторонам? На протяжении десятилетий ТБМ традиционно собираются на заводах, где компоненты собираются и испытываются, а затем разбираются и отправляются на строительную площадку. Доставка машины часто может быть критическим путем, влияющим на график проекта, стоимость, рабочую силу и другие факторы. Первая сборка на месте (OFTA) была разработана и использовалась в десятках проектов по всему миру, чтобы обеспечить экономию средств и времени подрядчикам, работающим над быстро развивающимися проектами в сжатые сроки. Использование OFTA растет, что позволяет первоначально собирать ТБМ на строительной площадке и сокращать дополнительные этапы транспортировки и разборки. В этом документе будут проанализированы причины сборки в цеху по сравнению со сборкой на месте, определены конечные преимущества и недостатки каждой из них. В документе также будут проведены количественные сравнения с точки зрения времени и денег, а также различий в выбросах углерода, энергии и потребностях в рабочей силе. Документ завершится обсуждением современных тенденций в сборке ТБМ и будущих направлений строительства этих сложных проходческих машин.
1. ВВЕДЕНИЕ
Традиционно компоненты туннелепроходческих машин доставляются в большой сборочный цех, собираются, испытываются, разбираются, транспортируются на рабочую площадку и снова собираются на месте перед началом работы. Для сравнения, другое крупномасштабное промышленное оборудование редко полностью предварительно собирается и тестируется перед установкой в ??конечном предполагаемом месте. В качестве примеров рассмотрим малые и средние газовые электростанции, роторные экскаваторы и небольшие специализированные производственные предприятия. Как и в машинах для бурения туннелей, для всех этих примеров время имеет существенное значение. В период от заказа оборудования до ввода оборудования в эксплуатацию ничего не производится, и денежный поток для подрядчика может быть отрицательным. Хотя устранение первых трех этапов процесса (заводская сборка, испытания без нагрузки и разборка) не приводит к 100% эквивалентной экономии времени и труда, это приводит к существенной экономии и того, и другого. Кроме того, есть экономия за счет снижения транспортных расходов.
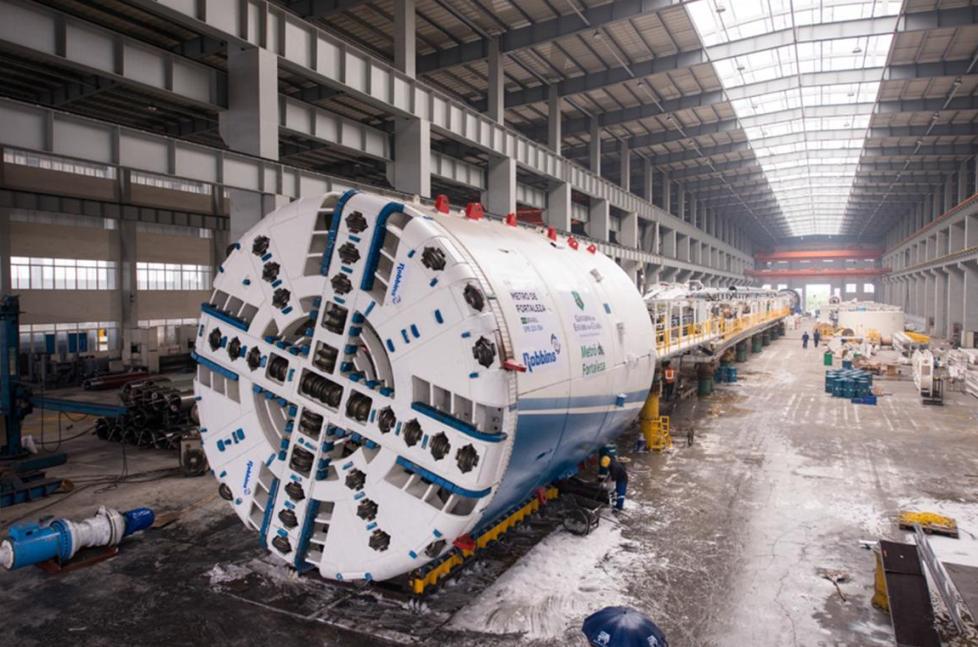
Фото: Пример первой сборки, испытаний на заводе
Учитывая сходство сложности и сроков поставки промышленного оборудования и оборудования для проходки туннелей, возникает вопрос: почему производители проходческих машин, строительные строители и владельцы проектов так долго сопротивлялись прямой доставке компонентов на площадку для первой сборки? Легко понять, почему производители машин, вложившие большие средства в стационарные производственные мощности, будут сопротивляться первой сборке на месте (OFTA), предпочитая статус-кво, при котором цены остаются высокими, а их производственные мощности заполнены оборудованием. Сложнее понять мотивы владельцев и консультантов. Даже сегодня, перед лицом растущих свидетельств преимуществ OFTA, многие консультанты продолжают указывать в тендерной документации, что проходческая машина должна быть полностью собрана и испытана на заводе. Это сопротивление OFTA может быть вызвано в целом консервативным характером владельцев проектов и их консультантов; однако, скорее всего, это простая привычка из прошлого. Настало время избавиться от этой привычки (см. Таблицу 1).
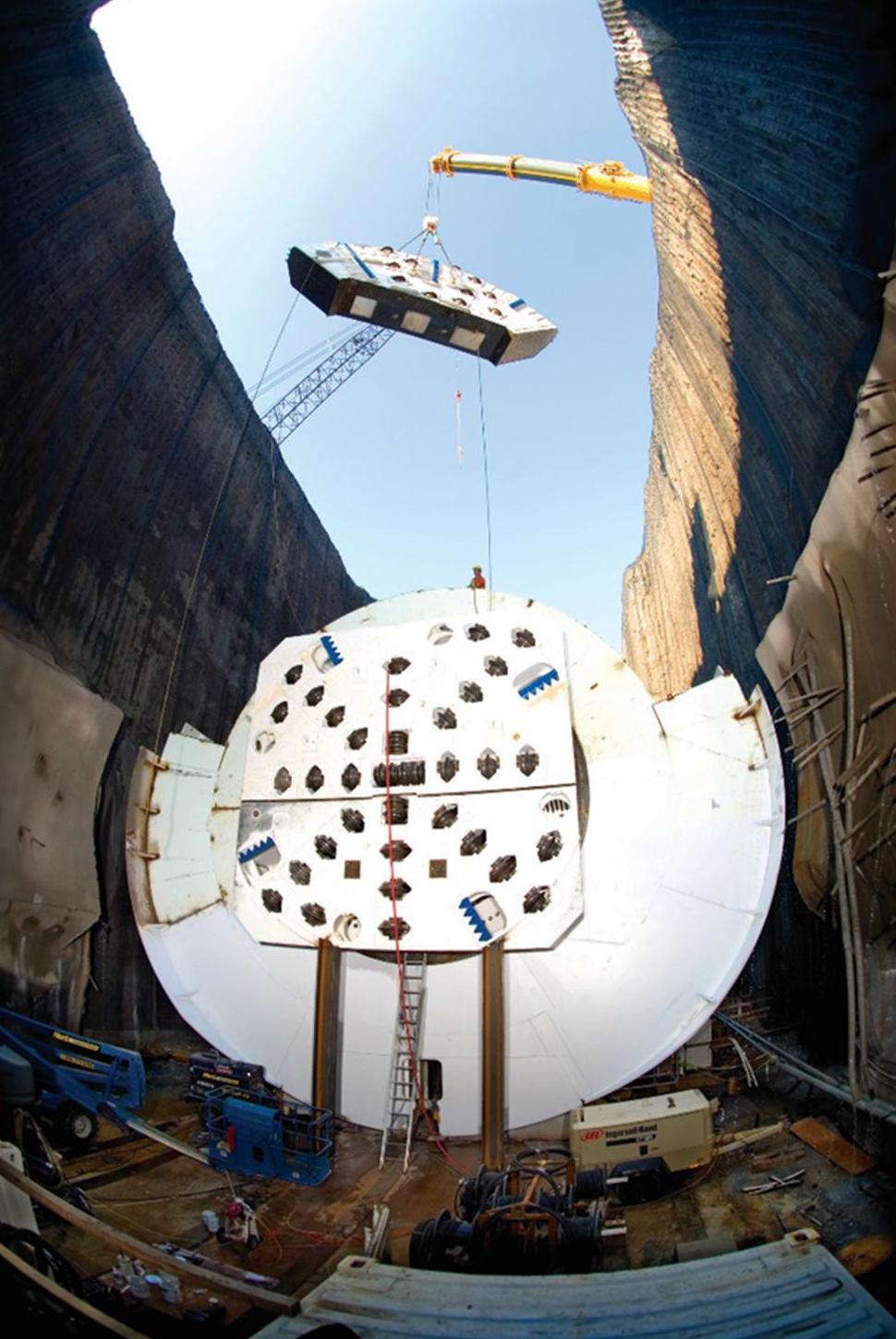
Фото 1: Пример первой сборки на месте, проект Ниагарского туннеля, Канада
1.1 Изменения в отрасли: реализованы преимущества OFTA
Тридцать лет назад проходческие машины проектировались вручную, на чертежных досках с карандашом и бумагой, а расчеты производились на старинных, по нынешним меркам, калькуляторах. Программное обеспечение для управления проектами было только мечтой. Двадцать лет назад ситуация несколько улучшилась, когда 2D CAD стали нормой, а первая волна программного обеспечения для управления проектами стала доступной. За последние 10 лет расширение 3D CAD и усовершенствование программного обеспечения для управления проектами, включая ссылки на многие программы планирования ресурсов предприятия/производства (ERP/MRP), предоставили производителям бесценные инструменты, с помощью которых можно обеспечить качество проектирования, соответствие изготовление сложных деталей и поставка сложных систем.
В ходе параллельной эволюции тридцать лет назад почти каждая тоннелепроходческая машина была уникальной по своей конструкции, изготавливалась по индивидуальному заказу и изготавливалась специально для каждого проекта. Сегодня такое бывает очень редко. Тридцать лет назад ежегодно производилось, наверное, несколько десятков проходческих комбайнов. Сегодня ежегодно производится в пять-десять раз больше тоннелепроходческих машин, и, как и другая тяжелая техника, многие из них имеют аналогичную марку и модель. В немалой степени благодаря обмену знаниями через профессиональные организации, такие как те, которые поддерживают эту конференцию, сегодня существует много общего согласия относительно «типа» проходческой машины, наиболее подходящей для определенных геологических условий. Стандартные типы: открытая твердая порода, одинарная или двойная защита для твердых пород, EPB и шламовая защита. В результате конструкция каждого из этих типов машин перешла от уникальной индивидуальной конструкции к сегодняшнему продукту значительно превосходящего качества, который имеет зрелую конструкцию и подлежит постоянному совершенствованию посредством постепенных изменений.
В результате такого совершенствования и эволюции проходческой машины, когда сегодня строительный подрядчик получает машину, очень высока вероятность того, что, как минимум, сердцевина машины была изготовлена ??много раз ранее. Это обеспечивает как более надежный продукт, так и возможность исключить стадию сборки на заводе с минимальным риском для всех участников.
1.2 Программа OFTA сегодня
Использование программного обеспечения 3D CAD сегодня позволяет точно проверять соответствие составных частей сложных машин на этапе проектирования. Тщательная и проверенная временем программа обеспечения качества гарантирует, что компоненты изготавливаются в соответствии с каждым чертежом, сохраняя гарантию на подгонку на следующем этапе производства. Доступность программного обеспечения для управления проектами (PM) с возможностью планирования и мониторинга ресурсов на протяжении всего процесса проектирования и производства, а также связь программного обеспечения PM с программным обеспечением ERP для всей компании предоставляет мощный инструмент для обеспечения того, чтобы каждый компонент эти сложные системы доставляются на место работы, когда это необходимо в процессе сборки.
Но для того, чтобы OFTA работала, нужны люди, опытные люди, а также программное обеспечение. Хотя это верно для всего процесса проектирования и производства, это особенно актуально на строительной площадке, где сложная проходческая машина должна быть собрана безопасно, быстро и правильно для достижения запланированного графика и экономии средств. К счастью, повсеместный глобальный рост использования всех типов туннельных машин за последние двадцать с лишним лет привел к появлению во всем мире высококвалифицированных специалистов по проходческим машинам. Где бы в мире ни находился проект, сегодня можно направить на место команду профессионалов, которые могут руководить сборкой и эксплуатацией любого типа машин.
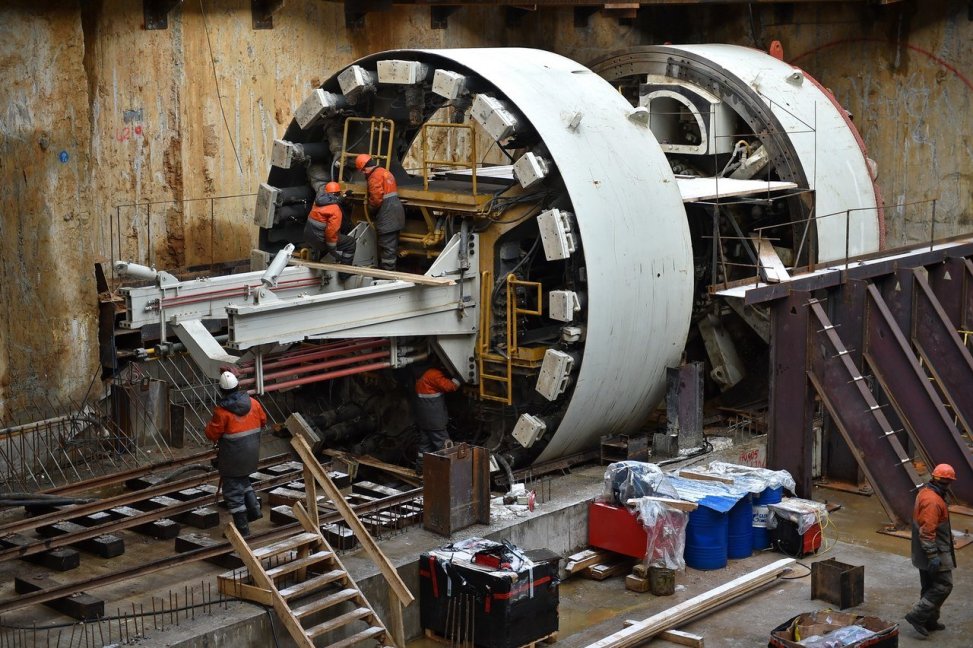
2. КОЛИЧЕСТВЕННАЯ ОЦЕНКА ПРЕИМУЩЕСТВ
В зависимости от размера и сложности производимой проходческой машины, а также от того, является ли машина новой или отремонтированной, экономия времени и затрат может быть существенной. На небольшой простой машине длиной 3,0 метра экономия времени может составить всего месяц или около того и, возможно, 5 000 человеко-часов и 100 000 долларов США на транспортных расходах. На сложной 10-метровой и более машине экономия времени может достигать нескольких месяцев, а также может быть сэкономлено 15 000 человеко-часов. Исключение транспортировки на завод для предварительной сборки таких больших машин может снизить транспортные расходы более чем на миллион долларов США. Однако отмеченное здесь снижение затрат, как правило, меркнет на фоне крупной коммерческой выгоды, связанной с реализацией крупного туннельного проекта в более короткие сроки.
Эти показатели экономии средств обобщены на основе предыдущего опыта проекта Роббинса. OFTA была впервые разработана и использована в 2006 году на крупнейшем в мире ТБМ с главной балкой, гиганте диаметром 14,4 м в проекте Ниагарского туннеля. С тех пор он используется на всех типах ТБМ и в различных местах по всему миру, от плотных городских районов до отдаленных и горных районов. Сводная информация о некоторой экономии времени и средств по этим проектам приведена ниже
Все оценки для этого исследования были подготовлены на основе EPB диаметром 8 м, предназначенного для строительной площадки в Лондоне. Таким образом, машина будет собираться либо на заводе в центральной части ЕС, либо непосредственно на стройплощадке в Лондоне. Эти параметры были установлены на основе имеющихся данных для сравнения, а именно отчета о выбросах углерода.
находки из туннеля Ли, часть проекта Thames Tideway Project в Лондоне. Для этого проекта требовалась машина диаметром 8 м, которая была собрана на заводе
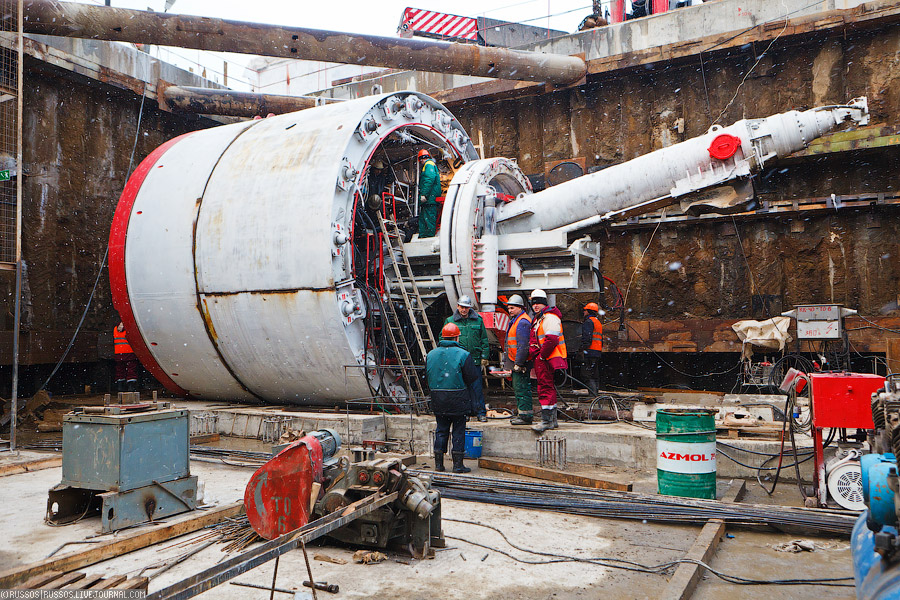
|
3.1 Преимущества времени
Что касается экономии времени, то прямая доставка комплектующих на стройплощадку должна сэкономить время по сравнению с процессом доставки в мастерскую, сборки ТБМ в мастерской, разборки и доставки на стройплощадку и, наконец, повторной сборки машины для запуска.
Основываясь на прошлых проектах, приведенная ниже временная шкала (см. Таблицу 3) представляет максимальную экономию времени, которая может быть достигнута за счет двух разных методов сборки. В этом случае весь процесс от закупки до изготовления, сборки, ОФТА, испытаний и, в конечном итоге, запуска ТБМ занимает около года. Для машины заводской сборки этот процесс занимает до четырех месяцев больше (один год и четыре месяца).
4. ВЫВОДЫ
Нельзя утверждать, что риск OFTA не увеличивается, но опыт показывает, что риск поддается определению, в значительной степени поддается контролю и, что наиболее важно, может быть снижен по мере накопления опыта. Основной риск, конечно же, связан с ошибками проектирования или изготовления, которые приводят к несоответствию компонентов во время сборки на месте. Этот риск снижается за счет использования предыдущих проектов, 3D CAD, внедрения надлежащих процедур проектирования и проверок, а также внедрения агрессивной программы контроля качества. Наконец, как показали поставки OFTA на сегодняшний день, когда возникают проблемы во время сборки на месте, график
может затянуться на несколько дней, но существуют методы восстановления потерянного времени. Коррекция на месте может быть выполнена с помощью специализированных производственных и механообрабатывающих компаний.
Ключевые компоненты успешной программы OFTA включают:
• Использование ранее проверенных конструкций, где это возможно
• 3D-дизайн и компьютерная проверка критических компонентов
• 100% контроль размеров критически важных компонентов на заводе-изготовителе
• Предварительная сборка подкомпонентов/модулей, когда это позволяет график или предварительная сборка не влияет на нее.
• Строгий контроль качества всех изготовленных компонентов для обеспечения правильной установки на месте.
• Абсолютный контроль над перечнем материалов всей системы проходческих комбайнов, чтобы гарантировать, что каждая часть, большая и малая, которая требуется для системы, отправляется на рабочую площадку.
• Логистическое планирование и контроль для обеспечения того, чтобы каждая деталь прибывала на рабочую площадку, когда она требуется, в порядке, необходимом для эффективной сборки и использования складского пространства.
• Планирование ресурсов для обеспечения того, чтобы все инструменты и персонал любого типа, квалификации и количества, необходимых для сборки, находились на месте, когда это необходимо.
• Предварительное планирование альтернативного восстановления, чтобы быть готовым быстро реагировать на возможные сбои на любом из вышеперечисленных шагов.
• Производитель машины должен предоставить большую, чем обычно, команду высококвалифицированного персонала для контроля и помощи при сборке на месте.
Владельцы проектов несут обязательства перед общественностью по строительству подземной инфраструктуры по конкурентоспособным ценам, в кратчайшие сроки и без неоправданного риска. Подрядчикам нужны все доступные инструменты для удовлетворения этих требований. Владельцам и подрядчикам тоннелей пора вступить в новое тысячелетие. OFTA предлагает возможность сэкономить время и деньги, как показало наше сравнительное исследование. Сокращение выбросов углекислого газа трудно поддается количественной оценке, но оно также проявляется в оптимизированном процессе доставки OFTA. Накопленный на сегодняшний день опыт доказывает, что OFTA можно реализовать с минимальным риском, используя современные инструменты проектирования, контроля качества и управления проектами. Приближается время, когда все участники будущих контрактов на строительство тоннелей должны пересмотреть требование о полной заводской сборке и испытаниях ТБМ перед доставкой на стройплощадку. Первоначальная сборка на месте — это практичная и эффективная альтернатива, позволяющая сократить затраты и время.
|