Разработка и проектирование режущих головок EPB
|
1. Введение
История и разработка туннельных машин для мягких грунтов имеет долгую историю, и поиски оптимальной конструкции для обеспечения безопасной и эффективной проходки всегда были главным приоритетом. Современная проходка тоннелей в мягком грунте началась с внедрения технологии шламовых ТБМ в 1967 году и разработки машин для балансировки давления грунта (EPB) чуть позже, в 1974 году, в Японии. С тех пор японские производители, а также североамериканские и европейские производители добились значительных успехов. Эти успехи были результатом уроков, извлеченных из успехов и неудач технологий в различных геологических областях. Во многих случаях философия японских и европейских производителей сильно различалась, что приводило к уникальным характеристикам машин. В случае с EPB и Slurry многие из этих достижений связаны с разработкой режущей головки, которая является первой частью машины, соприкасающейся с почвой. Конструкция режущей головки является неотъемлемой частью не только работы ТБМ, но и производительности машины. Надлежащая конструкция режущей головки должна учитывать различные переменные проекта, включая предполагаемую геологию и работу машины. Чтобы надлежащим образом определить и оценить характеристики режущей головки мягкого грунта, необходимо понимать, как эти характеристики развивались и как это применимо к геологии конкретной работы.
В этом документе будут рассмотрены основы конструкции режущей головки и то, как определенные атрибуты взаимодействуют с геологией и другими характеристиками машины для достижения эффективности земляных работ. Когда это возможно, будут рассмотрены сравнения между технологиями EPB и Slurry. Также будут проведены сравнения между различными школами мысли в отношении конструкции машин для мягкого грунта как в Европе, так и в Японии. Кроме того, объекты будут оцениваться на предмет потенциальных результатов при различных геологических условиях и методах эксплуатации. Глубокое понимание этих элементов позволяет использовать грамотный подход к максимальному увеличению скорости и производительности машины.
2. Основы конструкции режущей головки: коэффициент раскрытия
Помимо значений скорости вращения и крутящего момента, наиболее важным атрибутом режущей головки является ее коэффициент открытия, который определяется как количество открытой площади в структуре режущей головки, деленное на общую площадь режущей головки. Это соотношение оказывает большое влияние на то, как машина может работать в различных геологических условиях, хотя его влияние на производительность выходит за рамки простого значения. Это значение также, вероятно, наиболее заметное изменение, которое можно увидеть по мере развития технологии. Это также область, где со временем разошлись головки EPB и Slurry (см. рис. 1).

Рис. 1. Пример коэффициента открытия
2.1 Ножевые головки EPB
Самые большие изменения в конструкции произошли в режущих головках EPB, которые также имеют самые большие различия в коэффициенте раскрытия в зависимости от различных геологических условий, которые будут разрабатываться. Коэффициенты открытия в первых EPB, таких как первые машины для навозной жижи, были относительно небольшими по сравнению с сегодняшними EPB. Эта эволюция была в значительной степени связана с процессом проверки технологии. Требовалась высокая степень механической поддержки забоя на случай, если технология не оправдала себя, что, в свою очередь, соответствовало малому коэффициенту раскрытия, позволяющему потоку грунта проходить через режущую головку. Подрядчики и владельцы изначально не доверяли этому методу самостоятельного удержания лицевого давления. Метод EPB быстро зарекомендовал себя, и соответственно уменьшился воспринимаемый риск владельцами проекта и подрядчиками. В результате была сведена к минимуму высокая степень механической поддержки лица, что очень выгодно для метода EPB. Фактически, в идеальных условиях EPB вообще не требуется режущая головка для разрушения грунта на месте: именно переборка машины требуется для уравновешивания давления земли и воды при движении машины вперед. Чтобы эффективно сбалансировать эту силу, необходимо, чтобы датчики давления грунта в переборке могли точно считывать давление на поверхности разреза, а для этого измерения требуется соответствующий псевдоожиженный грунт и проводимость к забою. Положение режущей головки находится между датчиками EPB и режущей поверхностью; следовательно, за счет минимизации конструкции режущей головки давление на забое передается на датчики более точно, и поток материала меньше ограничивается. Эту философию можно увидеть во многих современных проходческих машинах, предназначенных для очень мягкого грунта.
2.2 Шламовые режущие головки
В случае машин для навозной жижи давление на забое не контролируется с помощью обратной связи от датчиков EPB. В зависимости от конструкции машины для поддержания постоянного давления на забое используются либо датчики давления, подключенные к переборке, либо давление воздуха, подаваемое в воздушный пузырь перед переборкой машины. Это означает, что высокий коэффициент раскрытия ножевого вала не так полезен для работы машины, как в EPB. Другой ключевой особенностью операций с шламом является образование глинистой или фильтрационной корки на забое выемки. После образования он действует как мембрана между грунтом на месте и относительно вязким навозом, позволяя навозу оказывать противодействие силам грунта на месте, контролируя при этом большинство материалов навоза. Есть несколько способов, которыми глинистая корка может быть скомпрометирована, и трудно узнать состояние забоя во время раскопок с помощью этих машин. Как только фильтрационная корка нарушена, давление в забое не так эффективно уравновешивается, и забой склонен к обрушению. Если режущая головка имеет низкий коэффициент раскрытия, что означает, что она предлагает высокую степень дополнительной механической поддержки, опасность, связанная с этим режимом отказа, сводится к минимуму. Японские производители, разработавшие технологию измельчения навозной жижи, не отказались от низкого коэффициента раскрытия режущей головки, так как конструкция развивалась с годами. По мере распространения технологии в Европе некоторые производители пытались использовать конструкции с более открытой компоновкой, подобные EPB, хотя со временем конструкция вернулась к более закрытой конфигурации лицевой стороны (см. рис. ниже).
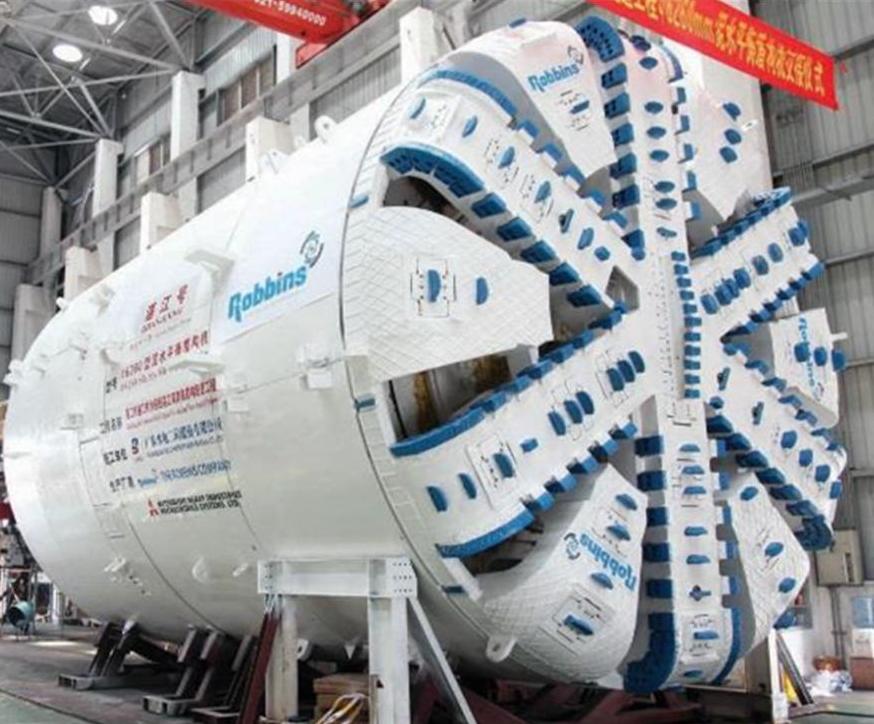
Рис. Современные шламовые ТБМ с малым коэффициентом раскрытия режущей головки
2.3 Структура отверстий ножевого вала
Понимая важность коэффициента открытия, особенно в машинах EPB, следует отметить, что не все отверстия создаются одинаково: форма и распределение отверстий также важны при оценке значения коэффициента открытия. Как и другие аспекты конструкции режущей головки, это следует рассматривать в отношении инструментов для выемки грунта, необходимых для ожидаемой геологии, и конструкции, необходимой для их поддержки (зная, что основной функцией режущей головки является поддержка режущих инструментов).
Как в шламовых, так и в ТБМ EPB отверстия служат путем, позволяющим материалу течь из забоя в смесительную камеру за режущей головкой и, в конечном итоге, из машины. Поскольку машины чаще всего имеют круглую форму, вынутый объем по сравнению с диаметром является квадратом, а это означает, что требуется более высокий коэффициент раскрытия по мере удаления от центра режущей головки к внешнему периметру режущей головки. В конечном итоге это хорошо работает по отношению к конструкции режущей головки, необходимой для поддержки инструментов для земляных работ. Инструменты расположены с равномерным радиальным интервалом, а это означает, что требуется меньше конструкции для поддержки инструментов по площади по мере удаления от центра. Центр, где теоретически должен требоваться самый низкий коэффициент открытия, в конечном итоге становится местом, где необходимо соблюдать особую осторожность.
При радиальном расположении инструментов на ножевой головке некоторые инструменты требуются в центре, что требует конструкции для поддержки этих инструментов. Чем выше нагрузка на инструмент, тем больше опорной конструкции требуется. Эта поддерживающая структура занимает большую часть площади в центре головы; на самом деле в большинстве случаев самый центр головы полностью поглощен структурой. При незначительном открытии или полном отсутствии отверстия в центральной части головки создается область локализованного высокого давления, которое может уменьшить текучесть грунта и способствовать уплотнению отверстий режущей головки, находящихся в непосредственной близости. За режущей головкой создается зона слабого потока, которая имеет тенденцию к затвердеванию. Эта тенденция была проверена в полевых условиях, так как центр режущих головок обычно забивается первым. Конечным результатом этой тенденции является то, что, хотя теоретически существует небольшое требование к отверстиям для навоза в центре, именно здесь должны быть сосредоточены усилия по проектированию, чтобы допустить некоторые отверстия при сохранении достаточной прочности.
По мере того, как геология становится все более твердой, либо в целом, либо с некоторыми твердыми элементами, такими как валуны, необходимы более агрессивные инструменты для разрыхления или разрушения грунта перед машиной. Помимо повышенных конструктивных требований к оснастке, более сложная геология создает проблемы с системами транспортировки породы, как по пульпопроводу, так и по шнековому конвейеру. Существует два основных метода обработки горных пород, с которыми можно столкнуться: первый заключается в том, чтобы позволить материалу попасть в режущую головку и обработать породу с помощью вторичных методов на машине. Во-вторых, управлять размером камней, которые могут попасть в режущую головку, путем дальнейшего закрытия режущей головки, чтобы позволить системе транспортировки навоза перемещать только те элементы, которые достаточно малы.
В первом случае, когда используются вторичные методы сортировки, такие как дробильная камера, как правило, меньшее влияние на конструкцию режущей головки для пульпы. На шламовых машинах коэффициент раскрытия уже относительно мал, что в первую очередь определяет размер элементов, которые могут попасть в режущую головку. Поступающие элементы могут обрабатываться дополнительным оборудованием, таким как дробилка, для дальнейшего уменьшения размера частиц. За счет относительно узких и длинных отверстий режущей головки для навозной жижи они лучше подходят для измельчения материала, сохраняя при этом достаточное отверстие для протекания навоза.
На машинах EPB эта опция вторичного дробления также не работает. Машины EPB спроектированы с большим коэффициентом открытия, что позволяет навозу беспрепятственно поступать в смесительную камеру. Это означает, что в смесительную камеру также попадают куски породы или валуны. Обычно шнековые конвейеры могут обрабатывать более крупные куски породы, чем шламовая машина, при этом самые большие валуны составляют примерно 1/3 диаметра шнека. Однако с небольшими ограничениями на то, что может пройти через головку, ограничения винтового конвейера могут быть легко превышены. В этих случаях винтовой конвейер может быть увеличен для захвата более крупных валунов, если это позволяет конструкция машины. Если это невозможно, то можно использовать ленточный шнек, который не имеет центрального вала и может работать с валунами примерно до 2/3 диаметра шнека. Ленточный шнек может работать сам по себе при низком давлении или в сочетании со шнеком с валом, чтобы обеспечить возможность удержания более высокого давления, что означает, что любые валуны должны быть удалены из шнека через отверстие для доступа, такое как ворота для сбора валунов.
Второй случай управления ограничениями размера материала в EPB требует, чтобы отверстия в режущей головке ограничивали размер частиц, попадающих в головку. Эти физические ограничения означают, что порода продолжает дробиться или перемалываться основными режущими инструментами до тех пор, пока она не пройдет через режущую головку и не сможет быть обработана системой транспортировки. Как отмечалось выше, это не так заметно на режущей головке для навозной жижи, но на EPB с высоким коэффициентом раскрытия эффект весьма заметен. Есть преимущества по сравнению с первым вариантом, поскольку он не рискует столкнуться с более крупным, чем ожидалось, валуном, который не может быть обработан конвейером. Это также не требует сложного удаления крупных камней с винтового конвейера. Однако есть и существенные недостатки: при уменьшенных отверстиях увеличивается переточка, что увеличивает износ режущих инструментов и режущей головки. Ударная нагрузка из-за участков скалы или валунов, находящихся перед головкой, также способствует увеличению износа. Уменьшенные отверстия дополнительно увеличивают сопротивление потоку, поэтому требуются более высокие концентрации кондиционирования грунта.
3. Форма режущей головки/влияние на глубину: плоская, полукупольная, купольная
Поток через режущую головку зависит не только от размера отверстия режущей головки, параллельного забою, но и от глубины режущей головки, которая перпендикулярна забою и через которую должна проходить кондиционированная порода. В идеальных условиях мягкого грунта это расстояние важно, но не особенно критично. По мере изменения грунтовых условий на смешанный грунт этот фактор становится все более важным. Смешанные грунтовые условия чаще всего увеличивают нагрузку на инструмент, что требует более глубокой конструкции режущей головки. То, как стенка туннеля формируется режущей головкой, также является важной частью определения требуемой глубины режущей головки.
Существуют три основные формы рабочей области режущей головки: плоская, полукруглая и куполообразная. Формы диктуются геологией. По мере усложнения геологии методы разрушения и разрыхления геологии начинают меняться. В мягкой геологии требуются только скребки для удаления материала с забоя и втягивания породы в режущую головку. По мере того, как геология становится более твердой, становится выгодным делать канавки в забое с помощью рыхлителей или долот с острой кромкой, чтобы скребкам было легче вытаскивать материал из забоя. По мере того, как материал превращается в горную породу, для добычи требуется другой механизм, прорезка, которая выполняется с помощью дисковых фрез, которые с большим усилием вдавливаются в твердый забой. Это действие вызывает трещины в породе, так что щепки выпадают между резцами. Установка требует больших расстояний между фрезами, поскольку они переходят от перпендикуляра к грани к параллельности к грани. Чем тверже порода, тем более постепенным должен быть этот переход, чтобы не перегружать какой-либо отдельный резец. Это изменение можно увидеть на рисунках 6-8 ниже, когда мы начинаем с плоской режущей головки и переходим к полукупольной головке, где дисковые резцы могут быть установлены в калибровочном положении, и, наконец, к куполообразной режущей головке, которая может работать с твердыми породами.
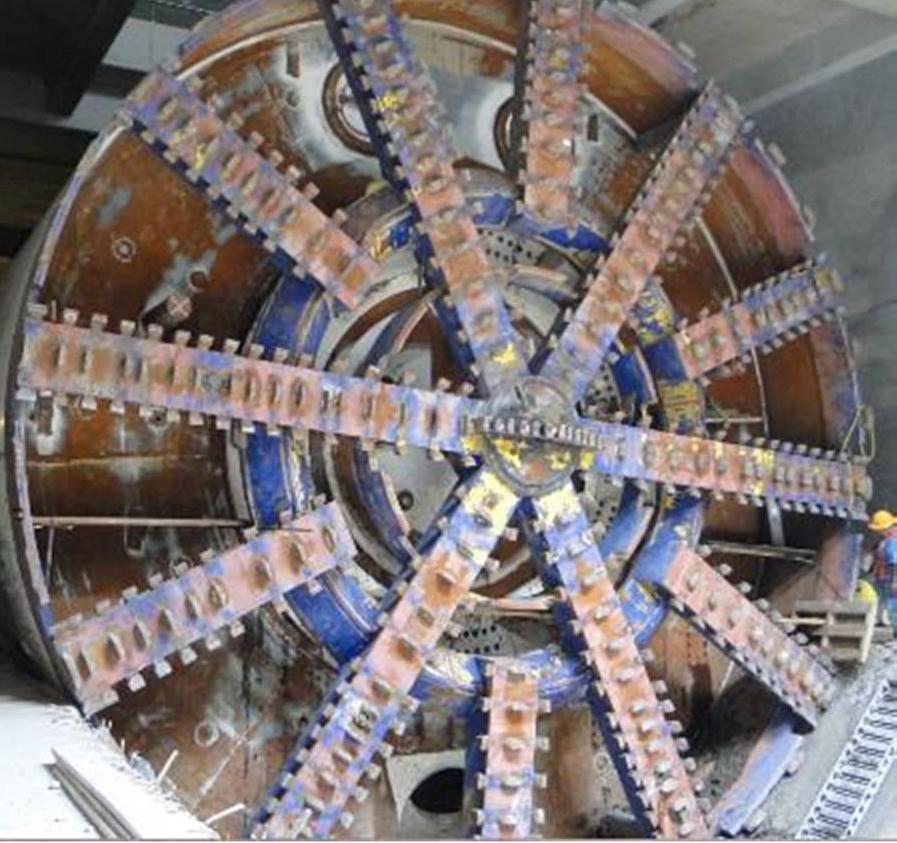
Рис. 6. Плоская режущая головка
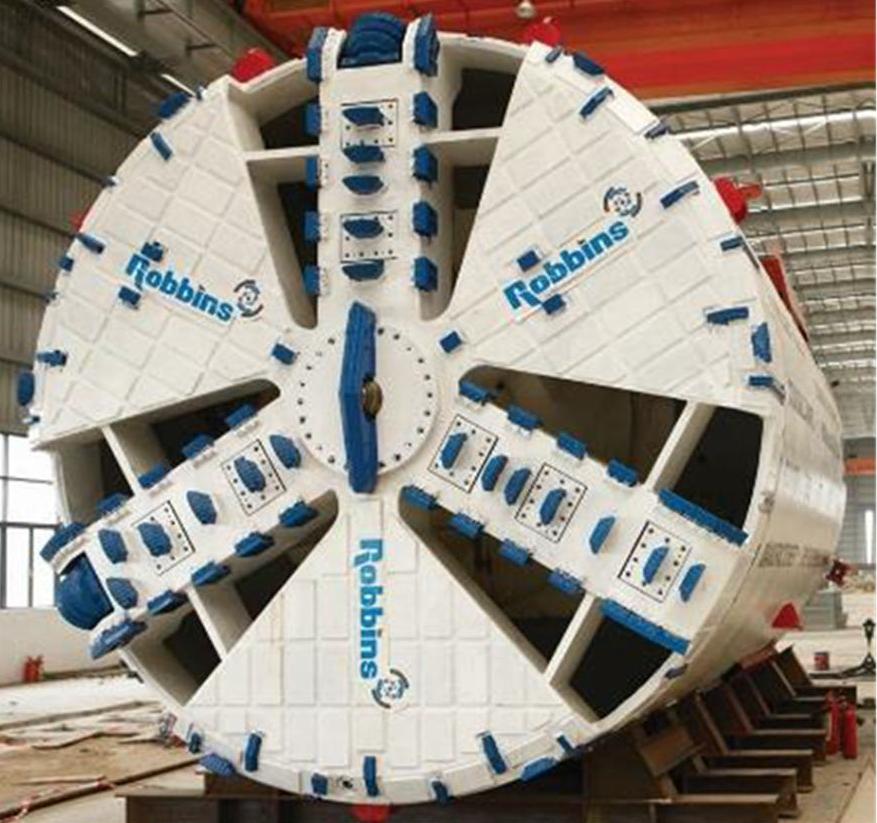
Рис. 7. Полукупольная режущая головка
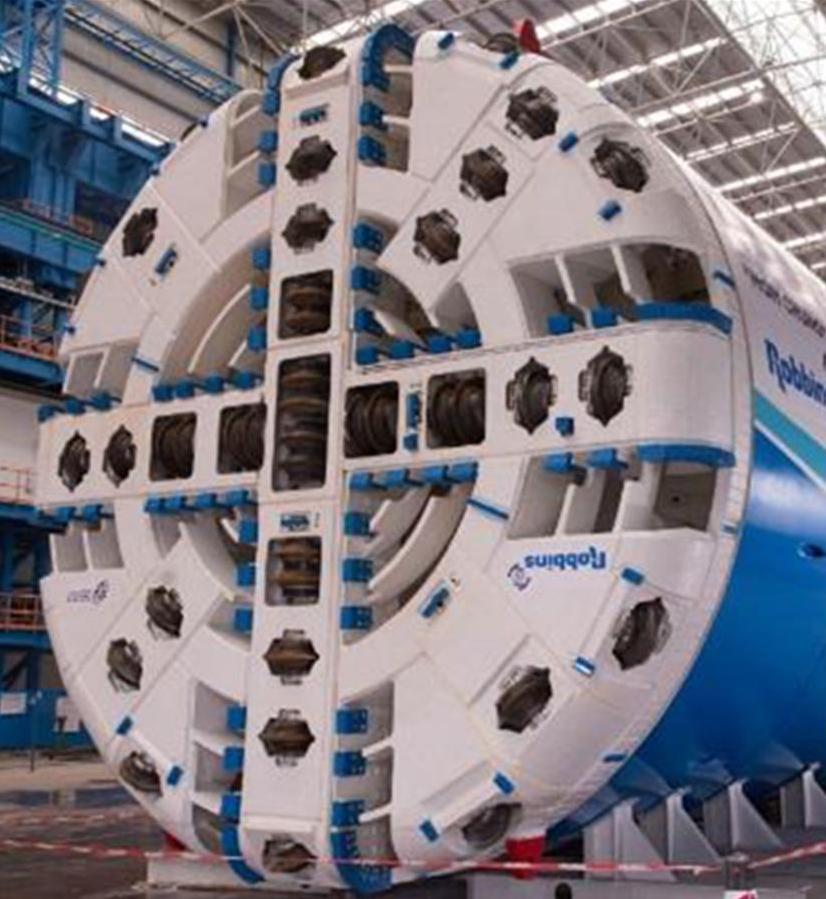
Рис. 8. Куполообразная режущая головка
Форма структуры, с которой сталкивается навоз при прохождении через режущую головку, также должна изменяться по мере того, как геология изменяется от мягкого грунта к смешанному грунту, содержащему камни или валуны. В чистых режущих головках EPB с высоким коэффициентом открытия оптимизация потока грунта может быть реализована с любой структурой, которая встречается, путем эффективного разделения потока по ее форме. Проблема с этим подходом, поскольку структура режущей головки становится более закрытой и увеличивается вероятность крупных элементов или валунов, заключается в том, что эта форма будет способствовать застреванию валунов или камней в конструкции. Это приведет к дальнейшему уменьшению коэффициента открытия режущей головки, а также может создать зону высокого давления в этой области головки, что вызывает особую озабоченность при использовании дисковых режущих инструментов, поскольку они имеют ограниченный рабочий диапазон давления из-за их уплотнения. Этот диапазон может быть расширен, если планируется, за счет использования дисковых фрез с компенсацией давления, хотя они не входят в стандартную комплектацию, поэтому необходимо предусмотреть такие условия. |
4. Режущие инструменты
4.1 Скребки
Скребки используются как в режущих головках для шлама, так и в режущих головках EPB, и они используются для втягивания геологии в режущую головку. В мягком грунте возможно, что они будут единственным инструментом, используемым для земляных работ. Скребки используют режущее действие, аналогичное режущему действию, наблюдаемому при образовании стружки при механической обработке металлов, где сформированная стружка представляет собой извлеченный материал. Наконечник скребка чаще всего изготавливается из карбида вольфрама, что обеспечивает высокую степень износостойкости в сложных условиях. По мере усложнения геологии возрастают и потребности в энергии для сдвига грунта, что ограничивает скорость проходки машины или увеличивает требования к крутящему моменту. Чтобы уменьшить эти требования к крутящему моменту при заданной скорости проходки, в забой наносится канавка с использованием долот с острой кромкой за счет уменьшения площади сдвига. По мере того, как геология переходит к мягкому камню или булыжнику, долото с острым лезвием берет на себя более важную роль в ослаблении геологии. Это ослабление создает более высокие нагрузки на инструмент, поэтому требуется инструмент с большим поперечным сечением.
4.2 Размещение скребка
Помимо конструкции самих скребков, их размещение на головке также влияет на их износостойкость и даже на желаемые параметры работы машины. Независимо от расположения важно, чтобы каждая часть режущей поверхности была закрыта в некоторой точке своего радиуса скребковым инструментом. Поскольку большинство головок поворачиваются в обоих направлениях, чтобы противодействовать крену машины, это необходимо делать для каждого направления или вращения. Такое расположение связано с тем, что сама почва очень абразивная — инструменты с твердосплавными наконечниками предназначены для работы в таких суровых условиях, но конструкция режущей головки или износостойкое покрытие не могут служить долго и быстро изнашиваются.
Поскольку существует множество различных конструкций режущих головок, особенно с EPB, мы рассмотрим две основные конфигурации скребков и эффекты, связанные с изменением конструкции с использованием одной и той же базовой конструкции режущей головки. В первом варианте скребки располагаются по обе стороны от основного режущего инструмента (лезвия/фрезы). Самым большим преимуществом такой компоновки является то, что контакт инструмента с землей на месте на противоположной стороне спицы сведен к минимуму, поскольку он был только что очищен. Это важное соображение, так как износ задней стороны инструмента может быть высоким, особенно если он не защищен карбидом вольфрама (как правило, это более дорогой тип инструмента). Во втором расположении инструменты, расположенные друг напротив друга, находятся дальше друг от друга. Если скорость ножевого вала остается постоянной, машина продвинется дальше к тому времени, когда задняя сторона второй спицы соприкоснется с родной почвой, вызывая более высокий износ. Таким образом, с точки зрения износа предпочтительно близкое расположение скребков «спина к спине» (см. рис. 9-10).
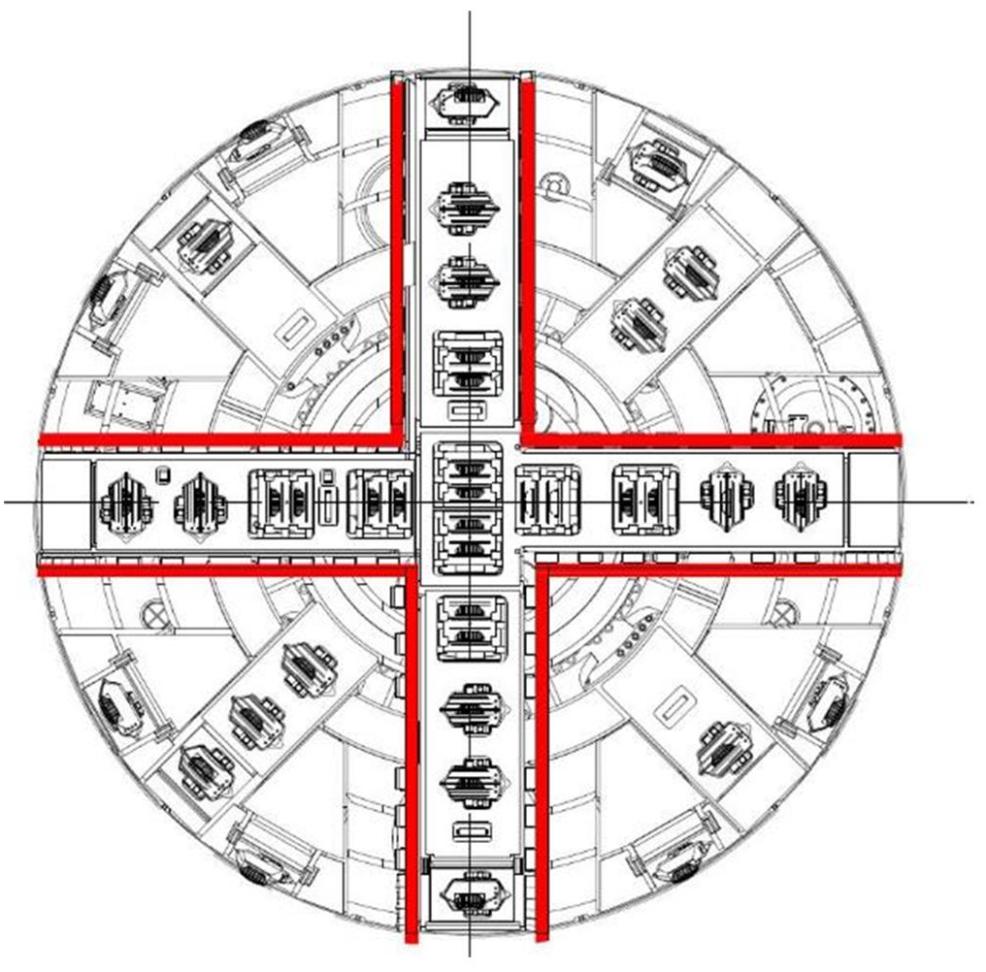
Рис. 9. Близкое расположение скребков
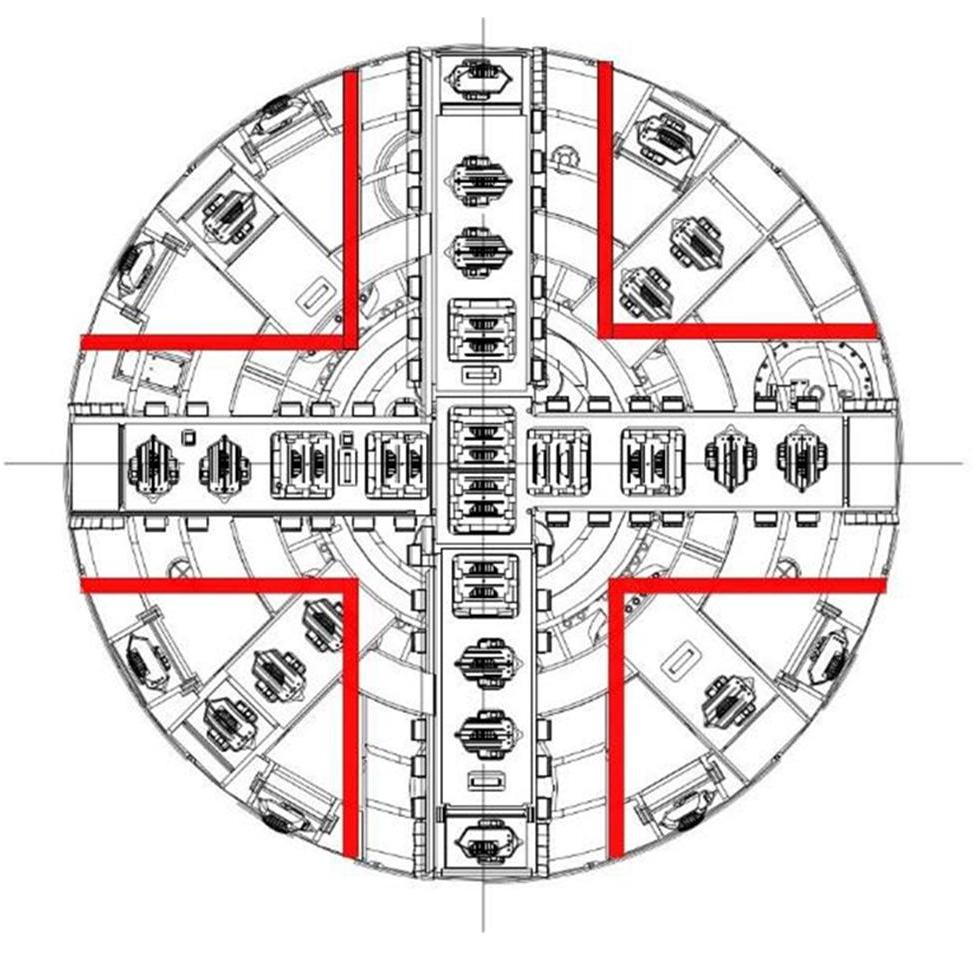
Рис 10. Широкое размещение скребков
Если машина будет эксплуатироваться без использования метода EPB или в открытом режиме, необходимо принять во внимание другие соображения. В открытом режиме торец стабилен, и для снижения требований к износу и крутящему моменту смесительная камера за режущей головкой не заполняется полностью. Если используются дисковые фрезы, то скорость подачи гораздо более тесно связана со скоростью режущей головки. По мере того, как материал втягивается в головку, он будет иметь тенденцию вытекать обратно в зону низкого давления на задней стороне спицы. Эта тенденция возрастает по мере увеличения скорости режущего вала. Режущая головка с более широким размещением инструмента лучше удерживает материал внутри.
смесительной камере, тем самым повышая эффективность навозоудаления и сводя к минимуму износ (см. рис. 11-12).
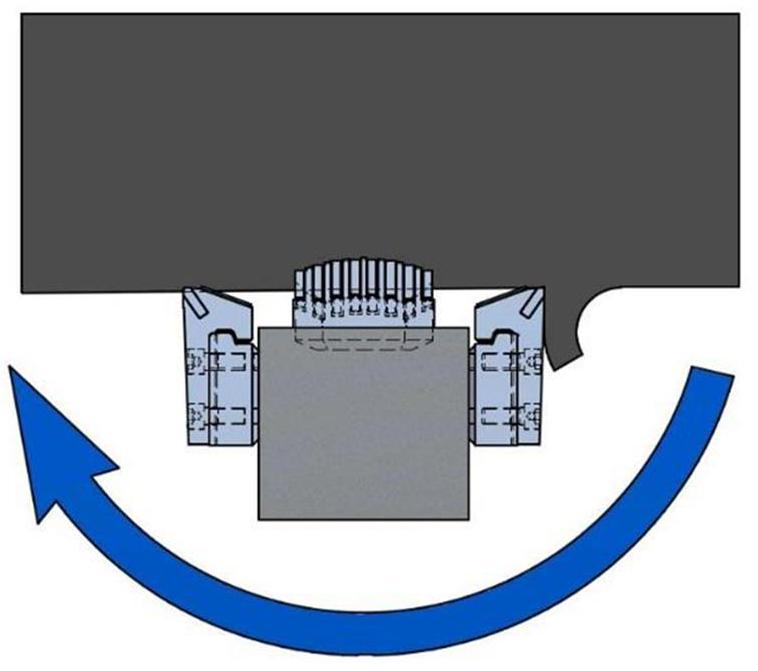
Рис. 11. Близкое размещение инструмента
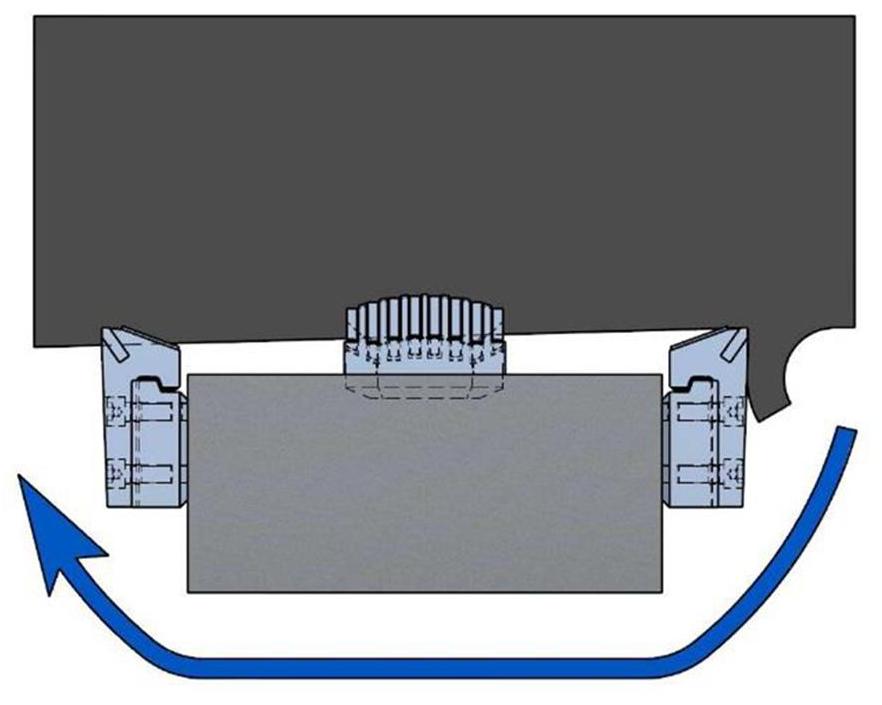
Рис. 12. Широкое размещение инструмента |
4.3 Дисковые фрезы
Дисковые фрезы за многие годы использования показали себя как лучший выбор режущего инструмента для дробления породы на более мелкие куски для легкого удаления. Однако простое использование термина «дисковые фрезы» не описывает все доступные типы дисковых фрез. Доступно множество типов дисков и множество вариантов конфигураций этих дисков на корпусе, вращающемся вокруг неподвижного вала.
Дисковые фрезы были впервые изобретены для разрушения горных пород и имеют самый долгий срок службы среди всех режущих инструментов в горных породах. Однако, когда дисковые фрезы используются в мягком грунте, их срок службы может быть неполным. Дисковые фрезы полагаются на силу, с которой машина контактирует с твердой поверхностью. При нормальной работе кольцо будет изнашиваться равномерно по окружности. Однако, когда дисковый резак не катится, только одна сторона кольца скользит по поверхности, и на передней стороне кольца образуются плоские участки. Кроме того, способность дисковой фрезы вращаться после образования плоского участка дополнительно затруднена из-за острой кромки, образующейся между плоской областью и остальной частью закругленного края кольца (см. рис. 13). Еще одно соображение при использовании дисковых фрез заключается в том, что, поскольку они вращаются, им нужны подшипники и используются уплотнения для защиты этих подшипников от суровых условий окружающей среды. Эти уплотнения имеют ограничения по давлению — биты с острой кромкой не имеют уплотнений и, следовательно, не имеют этого ограничения. Еще одно соображение относительно уплотнений заключается в том, что дисковые фрезы вращаются из-за взаимодействия между режущей поверхностью и кончиком фрезы. В мягкой геологии величина силы, которая может быть создана для эффективной земляной работы, может быть весьма небольшой. Однако с дисковыми фрезами требуемое усилие прокатки намного больше. Для предотвращения перепада давления между внутренним уплотнением и внешней зоной резания при давлении выше 4 бар была разработана специальная конструкция. На фрезу можно установить устройство компенсации давления для выравнивания давления внутри и снаружи фрезы. На рис. 14 показано поперечное сечение такой фрезы, в которой используются твердосплавные вставки в корпусе фрезы с наплавкой, а также имеется фиксатор, компенсирующий давление.
Специализированные фрезы должны быть дороже стандартных фрез, потому что они имеют дополнительные детали или улучшенные свойства материала. Эти затраты, вероятно, будут компенсированы более длительным срок службы этих типов фрез. Сокращение времени простоя, необходимого для смены фрез, а также риска каскадных отказов также снижает продолжительность и стоимость проекта.
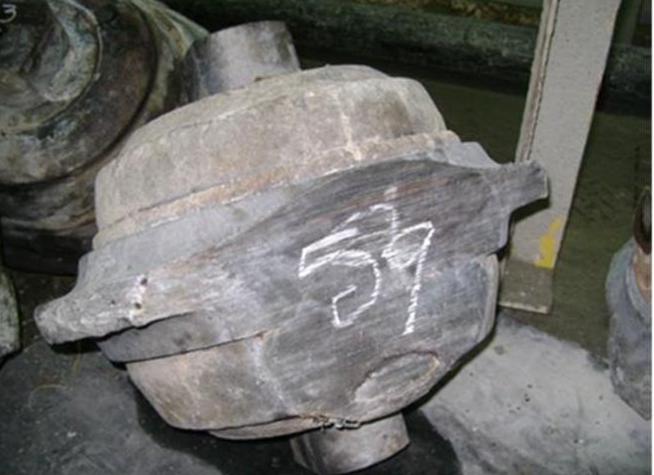
Рис. 13. Повреждение невращающейся фрезы
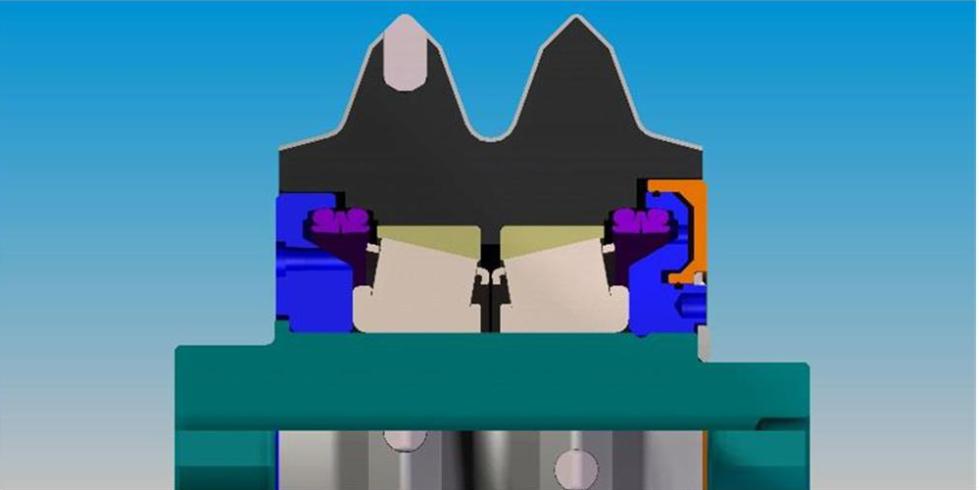
Рис. 14. Фреза с твердосплавной пластиной с компенсацией давления
5. Сравнение японской и европейской концепций дизайна
Каждый производитель станков имеет уникальные конструктивные особенности, когда речь идет о конструкции режущей головки, и для каждого производителя не существует единой окончательной конструкции. При этом, как говорится, можно рассмотреть две широкие категории концепций дизайна. Для машин для навозной жижи это более заметная разница, хотя, как упоминалось ранее, конструкция режущих головок становится все более похожей как в Европе, так и в Японии. Для машин EPB остается большая разница, поскольку японская философия имеет тенденцию предписывать машину, которая использует более низкую скорость режущей головки, но имеет более высокий установленный крутящий момент. Как обсуждалось в разделе 4, это приводит к близкому размещению скребков спиной к спине. Частично это связано с мыслью, что низкая скорость режущей головки снижает износ, сводит к минимуму потребность в добавках и сводит к минимуму помехи перед режущей головкой. Европейские машины, как правило, имеют более высокие скорости режущей головки, что сводит к минимуму необходимое проникновение и, следовательно, требуемый крутящий момент. Для эффективной работы с более высокой скоростью режущей головки и в открытом режиме очень часто используется более широкое расстояние между скребками.
6. Области для продвижения
Несмотря на то, что за последние 40 лет в конструкции режущих головок были достигнуты значительные успехи, остается еще много областей, требующих оптимизации конструкции. Большинство возможностей для улучшения будут продолжаться в области технического обслуживания и удобства обслуживания режущей головки. Во многих случаях эти достижения не будут новыми концепциями. Для некоторых это сделает существующие концепции более надежными или надежными, чтобы лучше выжить в сложной среде туннелирования. Для других это будет улучшение машин и режущих инструментов таким образом, чтобы они не были непомерно дорогими и могли использоваться более широко.
Основной причиной технического обслуживания режущей головки является проверка или замена режущих инструментов. Отличный способ сократить техническое обслуживание — увеличить срок службы инструмента. На это влияет множество факторов, поэтому можно использовать множество подходов, включая размещение фрезы на режущей головке, как обсуждалось ранее. Использование химикатов и добавок, таких как пена, является одним из подходов к увеличению срока службы инструмента. Еще одним является использование различных инструментальных материалов. Хорошим примером этого может служить конструкция режущих лезвий: выбор твердого сплава для использования в этом приложении затруднен, так как чем тверже материал, тем выше износостойкость, хотя это также делает резец более восприимчивым к сколам из-за удара. загрузка. Материал, который удерживает карбид на месте, также может изнашиваться настолько, что может выпадать целая стружка карбида, что обычно называют «гингивитом». Конструкция на рис. 15 использует ударную вязкость карбида E5 и износостойкость E2. С карбидом, образующим корпус инструмента, устойчивость к гингивиту очень высока. Хотя стоимость отдельного инструмента высока, он может быть экономически эффективным решением для правильной работы.
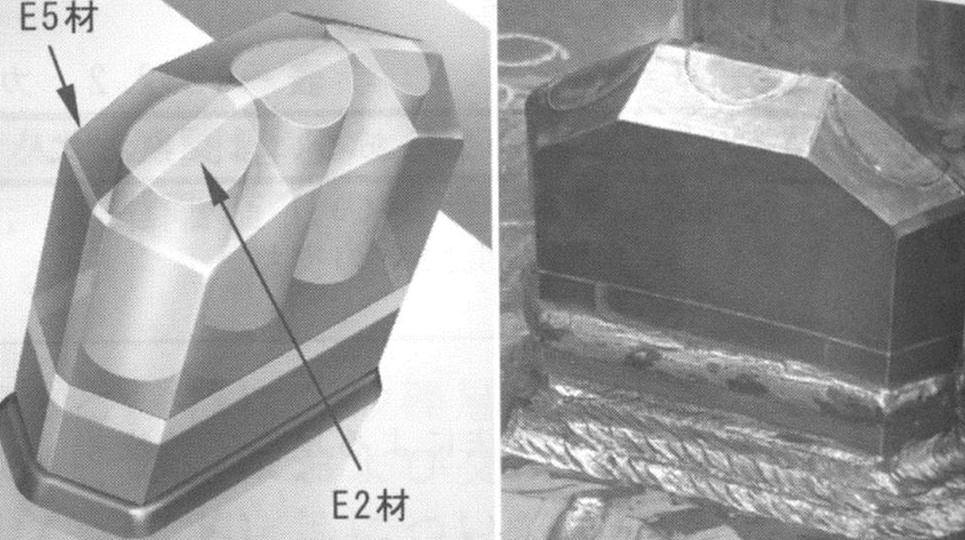
Рис. 15. Уникальная концепция твердосплавного скребка
Еще одна необходимая область для продвижения — часто трудный процесс проверки и замены инструмента под давлением. Чтобы свести к минимуму потребность в сложных проверках фрезы, особенно когда необходимо поддерживать давление на забое, в настоящее время доступно несколько методов. Одним из наиболее распространенных способов сделать это является использование долота для обнаружения износа, гидравлически подключенного к датчику давления, который подаст сигнал тревоги, если гидравлическое давление потеряно из-за отверстия в инструменте. В идеале, этот инструмент должен быть похож по конструкции на инструмент, который он пытается измерить, что обычно означает, что он будет использовать твердосплавные вставки и иметь твердое покрытие из того же материала, что и ножевые насадки.
Хотя это и не так полно, как осмотр бригадой смены фрезы, в сложных ситуациях может быть выгодно провести визуальный осмотр режущего инструмента без затрат на давление. Это можно сделать с помощью камеры номинального давления, установленной через перегородку машины. Это само по себе дает очень ограниченную информацию, поскольку внутренняя часть смесительной камеры обычно закрыта, так что визуальный осмотр невозможен. В сочетании с распылением воды под высоким давлением можно провести более качественную проверку. В этот момент доступ становится все более растущим преимуществом и затратами. Из единой точки контроля системы Возможности могут быть увеличены, чтобы можно было достичь диапазона визуального осмотра с помощью водяной струи.
Однако в какой-то момент инструменты должны быть заменены. Как и в процессе контроля, смена инструмента усложняется в условиях высокого давления. Чем выше давление, тем выгоднее иметь конструкцию, которую можно обслуживать без необходимости присутствия людей под давлением. Одним из подходов может быть использование промышленного робота вместо человека. Это рассматривалось в прошлом, но никогда полностью не применялось из-за соображений стоимости. Тем не менее, это достаточно убедительная идея, которая обеспечила некоторое финансирование исследований по заказу Европы. Другой базовый подход к смене инструментов заключается в том, чтобы донести инструменты до людей, которые находятся в атмосферных условиях. Это можно сделать, создав проходы в самом ножевом валу, которые не требуют давления и к которым можно получить доступ изнутри машины. Эта атмосферная система смены режущего инструмента обеспечивает гораздо более легкий доступ к инструментам, хотя, чтобы люди могли перемещаться по конструкции режущей головки, ее необходимо сделать глубже, чем обычно, что может быть вредным, как обсуждалось ранее. Также возможно повернуть всю режущую головку так, чтобы она оказалась внутри щита. Это позволяет не только получить доступ ко всем инструментам, но и ко всей конструкции режущей головки. Вращение требует, чтобы режущая головка каким-либо образом втягивалась, складывая или втягивая рычаги, что ограничивает конструктивные возможности. Механизм вращения и уплотнения также сложно изготовить в масштабе ТБМ, что еще больше увеличивает стоимость (см. рис. 17, экспериментальная машина, разработанная в Японии).
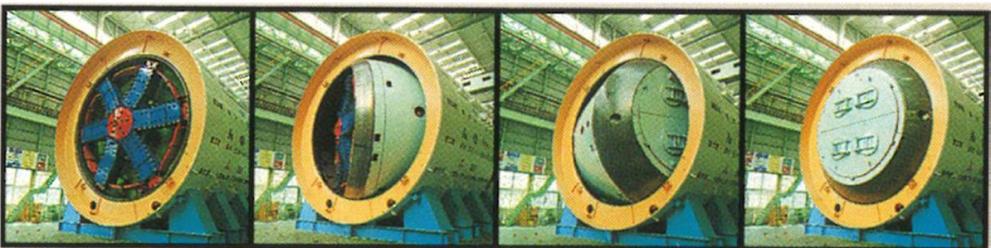
Рис. 17. Конструкция доступа к режущей головке с полным давлением. Предоставлено МХИ
7. Заключение
Машины EPB и Slurry значительно усовершенствовались за последние 40 лет. Это проявляется во многих различных аспектах машины и, конечно же, в конструкциях режущих головок. В то время как эти машины становятся все более зрелыми и понятными технологиями, они работают в очень сложных условиях, и остается еще много областей для улучшения в дизайне и реализации этих продуктов.
|
Весь комплекс генподрядных работ по строительству подземных сетей.
. // . ..................................................................... .ceo@микротоннелирование.рф
ПРОЕКТИРОВАНИЕ - ЭКСПЕРТИЗА - СТРОИТЕЛЬСТВО
Благодаря руководству, слаженным усилиям опытных проходчиков, шахтёров и ИТР сложные проекты реализуются качественно и точно в срок.
|